Expanding Tubes In Heat Exchangers, Condensers, & Other Heat Transfer Units

Selecting & Setting Up An Expander
Before you can start rolling, you will need to select the right expander for the job. Tube OD, and Wall/BWG will determine the size of the expander. However, there are some other factors to consider, such as tube projection, roll length, reach requirements, space constraints, and whether it’s minimum or average wall tubing.
Tube Projection
It’s important to consider if the tube is going to be expanded flush to the tube sheet or if it will have a projection. The most common tube projection for shell and tube heat exchangers is 1/8” from the tube sheet. In situations where all tubes will be rolled to the same projection, an expander with a recess collar should be used. This will accommodate the projection and prevent the tube from being pulled into the expander. The outlet side of surface steam condensers can have varying projections, up to 1X’s the tube diameter in length. In this case a telescoping or full recess collar should be used. If no tube projection is specified, the tube expander will come with a flush collar to expand the tube flush to the tube sheet.
Roll Length
Tube expanders come in two different roll lengths: short and long roll. In order to determine the correct roll length, you will need to know the tube sheet thickness. Choose the roll length that will expand the tube sheet area in the least amount of expansions. If expanding tubes in a double tube sheet, the inner primary tube sheet thickness must be specified so the expander’s rolls can be manufactured to allow for the proper effective expansion length. Whereas, the outer tube sheet would use standard rolls.
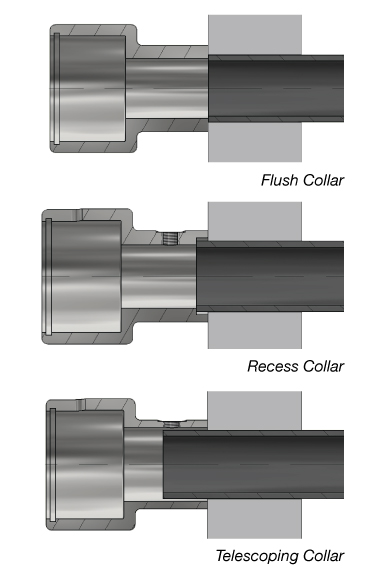
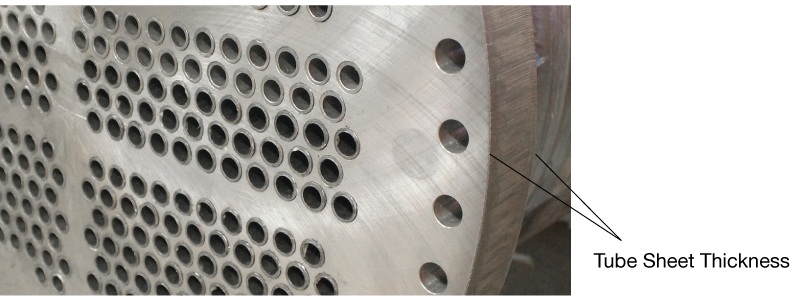
Reach Requirements
Generally, tube expanders come in 4”, 8”, 12”, and 18” reaches, but can be made longer to accommodate specific applications. For optimum tool life, use the shortest reach expander that will accommodate the application. Long reach expanders are used in heat exchangers with thick tube sheets or when reaching through water boxes, found in air coolers.
Space Constraints
Heat exchangers with channel boxes or division plates where the tubes are positioned too close to a wall for the expander’s collar to access perimeter tubes will require a friction collar. This collar is smaller in diameter than a standard collar, allowing more access to difficult areas. A friction collar should only be used as needed, as it’s not a replacement for a bearing collar.
Average Wall v Minimum Wall
When ordering tubes, it is very unlikely that each tube wall thickness will be exactly the same. Industry tolerances allow for ±10% thickness. That’s a total variation of up to 20% from the smallest to largest thickness, resulting in a wide range of sizes. For example, if you have .083” average wall tubes, the actual wall could be anywhere between .091” and .075”. If you were to buy a 14 BWG expander to fit .083, it would likely still work for either extreme due to the expansion range that the tool is capable of achieving.
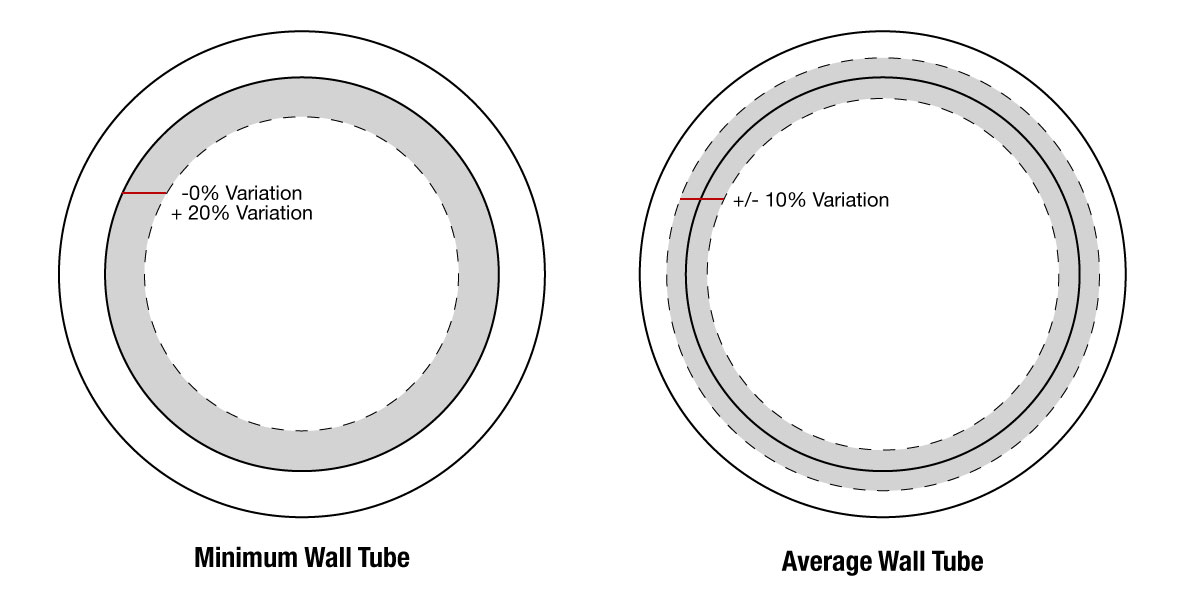
A min wall tube offers the same total variation in wall thickness that an average wall tube does, but the variation is applied differently. It allows for -0% and +20%. So the wall will never be less than the specified thickness. For example, a .083” min wall tube will range from .083” to .100” wall thickness.
At the upper end of that range, a normally sized tube expander will not have enough clearance to enter the tube. If you have min wall tubing, it is recommended that you drop down one expander size. So instead of ordering a 14 BWG expander, you would drop down to a 13 BWG. This ensures that the expander will fit inside of the tubes and still achieve the proper range of expansion.
Setting Up A Condenser Expander
Once the right tool has been selected, the tube expander’s collar will need to be set to the correct roll depth. Generally, you want to set the rolls 1/16” to 1/8” from the back of the tube sheet. This will ensure that the tool does not roll beyond the tube sheet. Simply, loosen the set screw on the collar, adjust the collar threads to the desired roll depth, and tighten the set screw on the expander’s cage flat. This will allow the expander to be adjusted to other depths if necessary.
Expanding Tubes
Once the collar has been selected and set, you can start expanding tubes. Using your predetermined wall reduction and calculated target ID, roll the first tube and check the finished tube ID. If the ID is over target, lower your torque value. If the ID is under target, increase the torque accordingly. Always expand an unexpanded tube when setting up. Once your target ID is achieved, go back and re-roll the initial setup tubes.
Step Rolling
In situations where the tube sheet is thicker than the length of the rolls, step rolling may be necessary. It is recommended to roll from the back of the tube sheet to the front of the tube sheet to allow tube growth to flow towards the operator or outside of the tube sheet. This will also help prevent the expander from putting stress on the tube and causing premature tube failure. Double radius rolls are recommended for step rolling. When rolling each step, you want to make sure the rolls overlap the previous step by 1/8” – ¼” for a smooth transition.
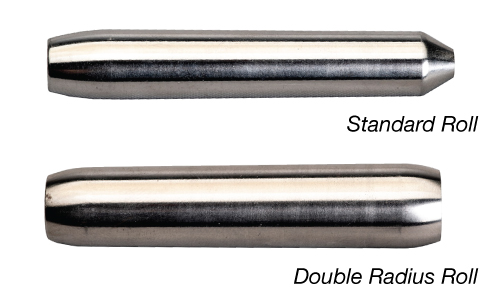
Keep Tube Expanders Clean And Cool
In order to get the best results and improve tool life, it is important to keep the expander clean and free from debris. There are two common types of lubricants that can be used for tube expansion: paste lubricant and liquid lubricant. While some operators have personal preferences with what type of lubricant they use, there are a few industry recommendations and standards to consider.
Liquid lubricant is often used on stainless steel or titanium tubes due to its low sulfur content. It is also commonly used in the electronic and nuclear industries. Paste lubricant, on the other hand, is commonly used in air coolers or other applications where the operator is reaching through the header box, as it doesn’t drip into the vessel. When using paste lubricant for copper and brass tubing, it is recommended to dilute the paste. Paste lubricant is also used when the operator wants to put lubrication in the tube prior to rolling.
Both lubricants prolong tooling by keeping the tube expander cool and preventing debris from adhering to the expander’s mandrel and rolls. A cooler cleaner tool will extend tool life by as much as 2 times.
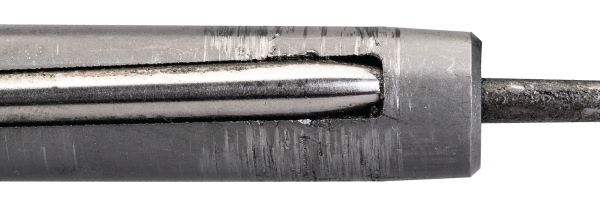
Expander Cage Wear
Watch For Wear
Replacement of damaged rolls and mandrels is necessary in order to eliminate tube leaks and damage to the tube or tube sheet. Proper maintenance of consumables also ensures no other parts of the expander become damaged.
Carefully inspect the length of the mandrel and rolls for scratches, pitting, galling, or spalling on the tapered surface and replace them if any irregularities are found. Since worn mandrels and rolls can damage other parts of the tool, it is important to replace worn or chipped parts immediately.
Parallel Pin Expansion
A traditional expander’s rolls are set at an angle to the mandrel, otherwise referred to as a feed angle. This feed angle causes a screw-like action that automatically feeds the mandrel into the tube as it rotates. With parallel pin expansion, the rolls are set parallel with the mandrel with zero feed angle. This means that the mandrel will not self-feed as a traditional expander would. Instead, the mandrel is pushed through the expander by force, in most cases hydraulic, causing the tube to expand.
There are two common reasons for choosing parallel pin expansion. The first is that it could reduce the stress on tube seal or strength welds. The second is that it is typically much faster than traditional tube expansion.
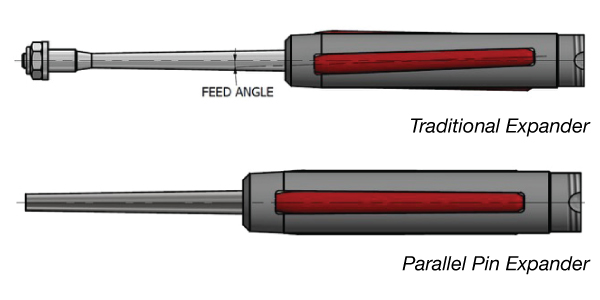
Some end customers are requiring manufacturers to use parallel pin expansion on seal welded tubes. They believe this process can better protect the integrity of the weld. In traditional expansion, the feeding of the mandrel introduces a pulling force on the tube, thus creating stress at the weld. With parallel pin expansion this force could be reduced or eliminated since the mandrel is being pushed into the tube and the rolls are being forced directly outward towards the tube wall.
Parallel pin expansion is significantly faster than traditional expansion due to the method in which the mandrel is pushed and pulled from the tube. In traditional expansion, the rotation of the mandrel combined with the feed angle determines how quickly a tube can be expanded; once the expansion is complete, the mandrel rotation must be reversed to remove the expander from the tube. Parallel pin expanders are constantly rotated in one direction while the mandrel is being pushed and pulled from the tube, independent to its rotational speed. This eliminates a portion of the time that a traditional expander needs to feed into and out of the tube, reducing the expansion cycle time by 50%.