Materials, Tube Leaks, & Pre-Expansion Steps
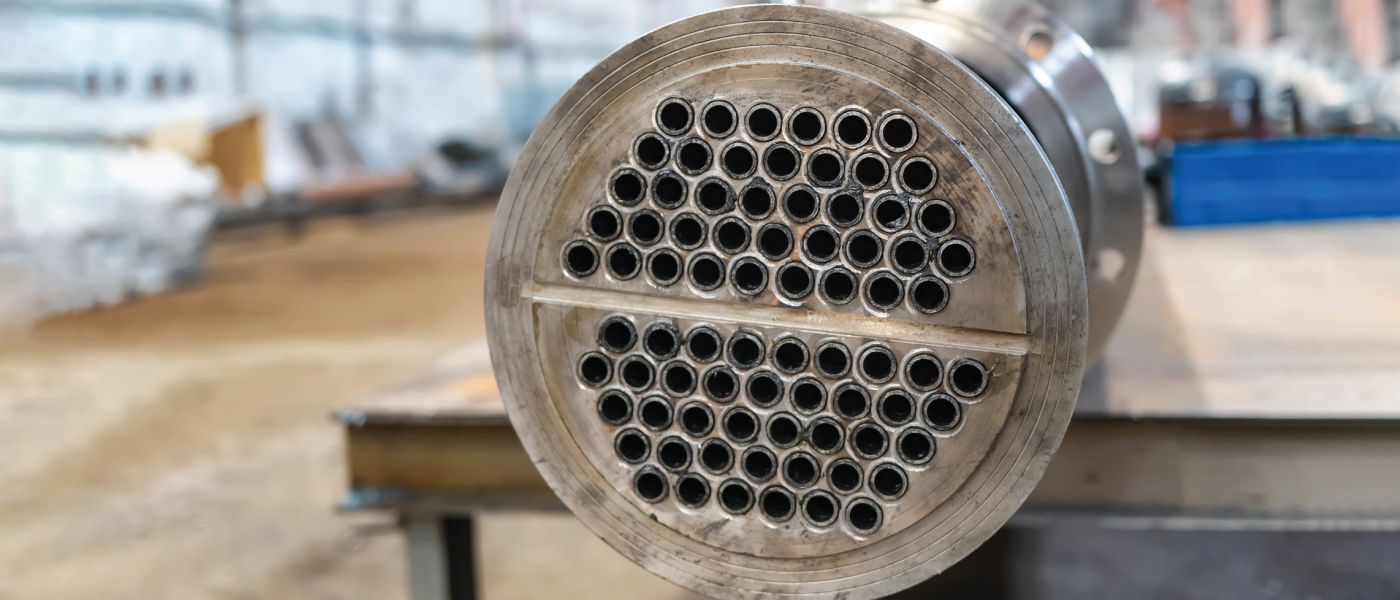
Tubing Material
Below are materials and percentages that can be used as a guideline when rolling tubes of like materials. In general, you want to roll to the lowest wall reduction possible where a tight tube to tube sheet joint can be achieved. The harder the material the less wall reduction required to obtain a tube joint. You should always consult the manufacturer of the heat transfer vessel for specific information before undertaking any maintenance procedures.
Material | TEMA Standard Target % Wall Reduction | API-660 Target % Wall Reduction | Description |
---|---|---|---|
Aluminum 3003 or 4004 | 4 – 6% | 5 – 7% | – |
Aluminum 6061-T | 6 – 9% | 8 – 10% | Used in aircraft fittings |
Carbon Steel & low-alloy steel (max 9% Chromium) | 5 – 8% | 8% max* | Tends to work harden quickly |
Stainless Steel and high-alloy steel | 5 – 8% | 6% max* | Tends to work harden quickly |
Duplex Stainless Steels | 4 – 6% | Not Specified** | Tends to work harden quickly |
Titanium (and other nonferrous, work hardening materials) | 4 – 6% | 5% max* | Tends to work harden quickly |
Admiralty Brass (and other nonferrous, non-work hardening materials) | 4 – 9% | 8%* | Over rolling may cause leaks, splits, or flaked tubes |
Copper & Copper Alloys | 7 – 10% | Not Specified | Soft but can be abrasive to the tube expander |
*API-660 lists maximum tube wall thickness reduction values only. For some materials, API-660 allows the wall thickness reduction to be increased by an additional 2%, if approved by the purchaser.
**Maximum tube wall thickness reduction to be agreed between the purchaser and vendor.
Tube Material Properties
Metals such as Titanium, Stainless Steel, and other exotics tend to work hard very quickly due to their elasticity. Elasticity refers to a material’s ability to stretch and return to its original state. Materials behave elastically until the force increases beyond the material’s elastic limit, meaning it cannot return to its original shape. During the expansion process, the tube material and tube sheet hole will expand until the tube reaches its plastic state and is contained by the tube sheet’s elastic properties.
Major Causes Of Tube Leaks
Tube leaks are usually caused by under-rolling, over-rolling, improper preparation of tube sheets, and differential thermal expansion. Improperly rolled tube joints can cause several challenges, such as necessary reworking and loss of vessel efficiency.
Under-Rolling Tubes
Under-rolling occurs when the proper amount of wall reduction is not reached. If left uncorrected, this will cause leaks between the tube OD and tube sheet hole ID. Under-rolled tubes can usually be fixed by rolling a second time to obtain the proper amount of wall reduction. Be sure to use a tube gauge to periodically check the amount of wall reduction during rolling.
Over-Rolling Tubes
Over-rolling of tubes occurs when the expansion of the tube surpasses the expansion required for the proper wall reduction. Over-rolling can cause considerable damage to the tube sheet and adjacent tubes. Once a ligament is over-rolled, it will deform the ligaments of the tube joints surrounding it. This deformation can cause adjacent tubes to leak.
In addition to impacting tubes, over-rolling can cause distortion in tube sheets or drums. Over-rolling can potentially cause a tube sheet to bow or warp to the point where the standard length tube could not be used in the vessel until the bowing is returned to normal. This can be corrected in some cases by placing stay rods in the vessel and pulling the tube sheets back to their original position.
Lastly, over-rolling can have a significant impact on expander tool life. It can cause the tube material to flake off, which can get trapped in
between the rolls and mandrel. If this debris is not cleaned from the expander, it can reduce the life of the rolls and mandrel.
Over-rolling tubes is not something that can be easily corrected. Once ligaments become deformed, the entire tube sheet has an increased chance of leaks, higher maintenance costs, and decreased efficiency. As a result, it is important to avoid over-rolling by using an electronic or pneumatic torque control or an assisted rolling system. These systems will ensure you roll to an exact wall reduction every time.
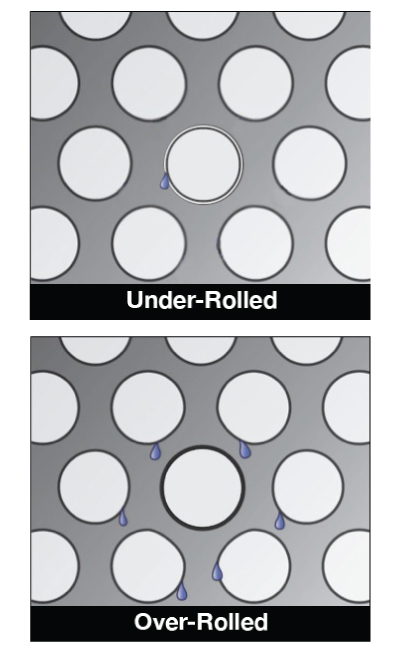
Improper Preparation Of Tube Sheet Holes
The smoother the tube seat or tube hole, the easier it is to roll an optimum tube joint. If the tube sheet or drum is gouged, it is extremely hard to expand the tube to fill these gouges without over-rolling. It is important that light ligaments and thin tube walls are mated to a tube hole that has a low micro range finish. Many manufacturers today are drilling, reaming and sizing or burnishing to get the micro-finish desired for tube holes.
Differential Thermal Expansion
Expansion due to heat varies noticeably between a thinner tube and the tube sheet, a shift of the tube results. One of the most important steps for guaranteeing a safe and permanent tube joint is to thoroughly clean the surfaces of the tube end and the tube hole wall. These two surfaces must be clean and free of all dust, mill scale and pits or scratches. Note: It is extremely important to eliminate any longitudinal scratches or cracks in the tube sheet hole wall. These longitudinal lines will cause leaky tubes.
Pre-Expansion Steps
Preparation of Tube Sheet Holes- Heat exchangers / condensers
- Drill and ream tube sheet holes to TEMA or ASME codes.
- Be certain the tube sheet material and ligaments are sufficient to guarantee a safe and permanent tube joint.
- When conditions permit, utilize a sizing or burnishing tool to further assure a good finish in the tube hole. This will also slightly increase the tensile strength of the ligament.
- The serrations or grooves to be used will determine the joint strength of the tube joint. It is extremely important when retubing that the grooves be cleared of all metals or any foreign material.
Preparation of Tube Sheet Holes – Drums / Tube Sheets / Headers
- Tube holes are normally drilled and reamed to comply with API, ASME, or National Board Inspection Code.
- It is extremely important during this operation that there are no longitudinal scratches or cracks left in the tube seat.
- In cases where out-of-roundness is extreme, pre-rolling of the tube holes is advised.
- Be certain that the tube hole walls and the grooves in the tube walls are cleaned down to bare metal before tubes are inserted. Be certain all-foreign material such as oil, grease, rust, or just plain dirt are removed. Special attention during this cleaning will prevent serious trouble later.
After tube holes have been prepared they are usually coated with a rust preventative compound. Before inserting any tube it is important to remove all traces of this coating. It is extremely important that great care be taken in handling the tubes for insertion in all of the vessels discussed above. Be certain that the tube ends are clear of any foreign material. Be especially certain that there are no chips on the tubing which may gouge the tube sheet or tube seat when the tube is placed in the vessel.
In some cases, it will be necessary to force a tube into a tube hole. This should be done with care. It is better to spring the tube than to try to force it with a hammer. If a tube end is kinked or damaged before rolling, the expanded end will be damaged and a leaky roll joint will result. Attention at this time to the tube ends and the tube alignment will prevent future troubles. It may be helpful to employ the use of a Tube End Setting Tool to properly set the tube in the sheet.
Pre-Expansion Tools
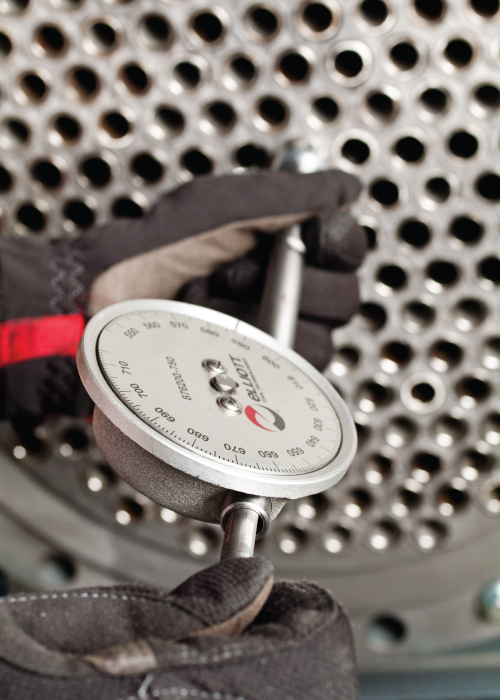
In order to create a better mechanical joint, it is important that the appropriate pre-expansion tools are used.
Tube Hole Gauges
Tube Hole Gauges make it easy to accurately measure tube IDs and tube sheet holes. Accurate measuring of tube holes ensures that expansion requirements are being met resulting in a mechanical joint. Proper mechanical joints ensure that the vessel is built to applicable engineering
standards and to maintain the efficiency and safety of the vessel.
Tube Sheet Hole Brush
Prior to rolling, it is important that tube hole surfaces are free of debris and minor scratches. A tube sheet hole brush can aid in the cleaning of these ID surfaces by removing dirt and deposits from tube sheets in surface condensers and heat exchangers. Clean tube sheet holes help to minimize
the possibility of leak paths during expansion.
Grooving / Serrating Tool
Grooving tools, also known as serrating tools, can be used in milling or drilling equipment for OEM tube sheet hole preparation. These tools provide
consistent diameter and depth of grooves in the production of the machined tube sheet holes.
Tube Pilots / Guides
Tube pilots, also known as tube guides, are used to pilot replacement tubes through tube sheets and tube sheet support plates that are commonly found in heat exchangers or surface condensers. The tube guide head is designed with a shoulder for the tube to rest against, eliminating the possibility of bending the tube end as the guide pushes through the support plates.