Ins and Outs of Roller Burnishing
3 Considerations When Selecting the Right Tool
Roller burnishing is a quick and effective method for achieving smooth surface finishes on metal work pieces. With a variety of burnishing tools on the market, it can be challenging to determine which will work best for a specific application. From multi-roll tools to diamond burnishing, each style is designed to provide a very fine finish, increase surface hardness, and reduce the need for multiple finishing operations. To choose the right tool, it’s important to understand how each works, the limitations of the tool, and the variations available. In this article, we will cover a few defining questions to ask to arrive at the right style of tool.
Define the Part Type
Determining the part type and the area that needs to be burnished is the first step in choosing the type of tool required. For example, burnishing the exterior of a valve body will be different than burnishing the ID of a cylinder. When burnishing internal bores, a multi-roll style tool is generally going to be the most effective, as it helps maintain the size of the bore and can produce a very low surface finish. For external diameters, faces, tapers, and radii, carbide roll burnishing tools will be the best option, as they are the most versatile tools.
Bore Depth & Type
For internal burnishing applications, the depth of the bore and finished area are necessary in choosing the right roll type. Overall, there are 3 main types of roll styles for internal burnishing: Through, Blind, and Bottoming rolls. In open hole applications like lamination stacks, through style rolls would be the best option. This means that there is nothing obstructing the path of the tool as it burnishes the through hole. In situations where you’re burnishing an enclosed space, like a piston rod, blind or bottoming rolls should be used. The difference between these two styles depends on the desired burnished depth of the hole, as shown in figure 1.
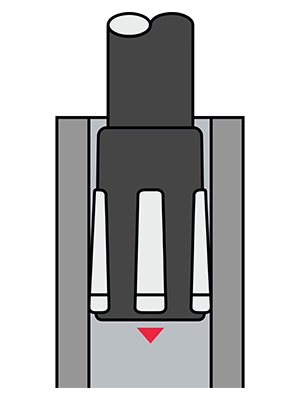
Through Rolls
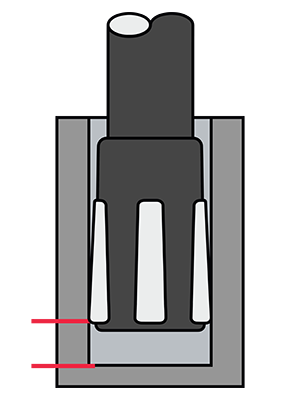
Blind Rolls
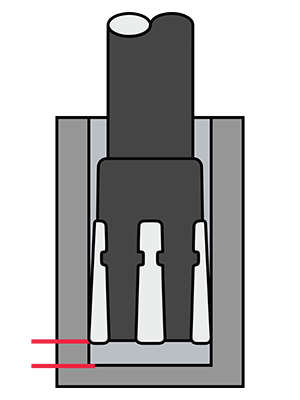
Bottoming Rolls
In addition to the type of hole, the depth of the hole is also important to know to determine the appropriate reach of the tool. Depending on the tool, longer shanks or additional extensions can be used to meet the required reach.
Machine Type
Identifying the machine that the tool will run on is necessary when determining the appropriate shank style or “hand” placement. The “hand” refers to the side that the tool mounts on in relation to the part that is being burnished, either the right or left. Additionally, depending on the machining application, it may narrow down the type of tool that can be used. For example, some tools require the part to spin, while others only work if the tool is rotating. As a result, it’s important to understand the application and the machine the tool will be operating on.
Overall, choosing the right roller burnishing tool will depend on several different factors such as, the part type, bore characteristics, and the machine it will be used on. Understanding these different features and how they apply to your application will allow you to select a tool that is the best fit for the application.
Read more about selecting the right burnishing tool by checking out other articles in this series: