What is Burnishing?
Comparing Burnishing to Traditional Finishing Methods
Metal Finishing refers to a wide range of processes that are aimed towards improving performance and minimizing wear over time. This can include everything from cleaning to deburring to surface finishing, depending on the part and end use application. In this article, we will be reviewing different types of surface finishing techniques and the benefits that each can provide.
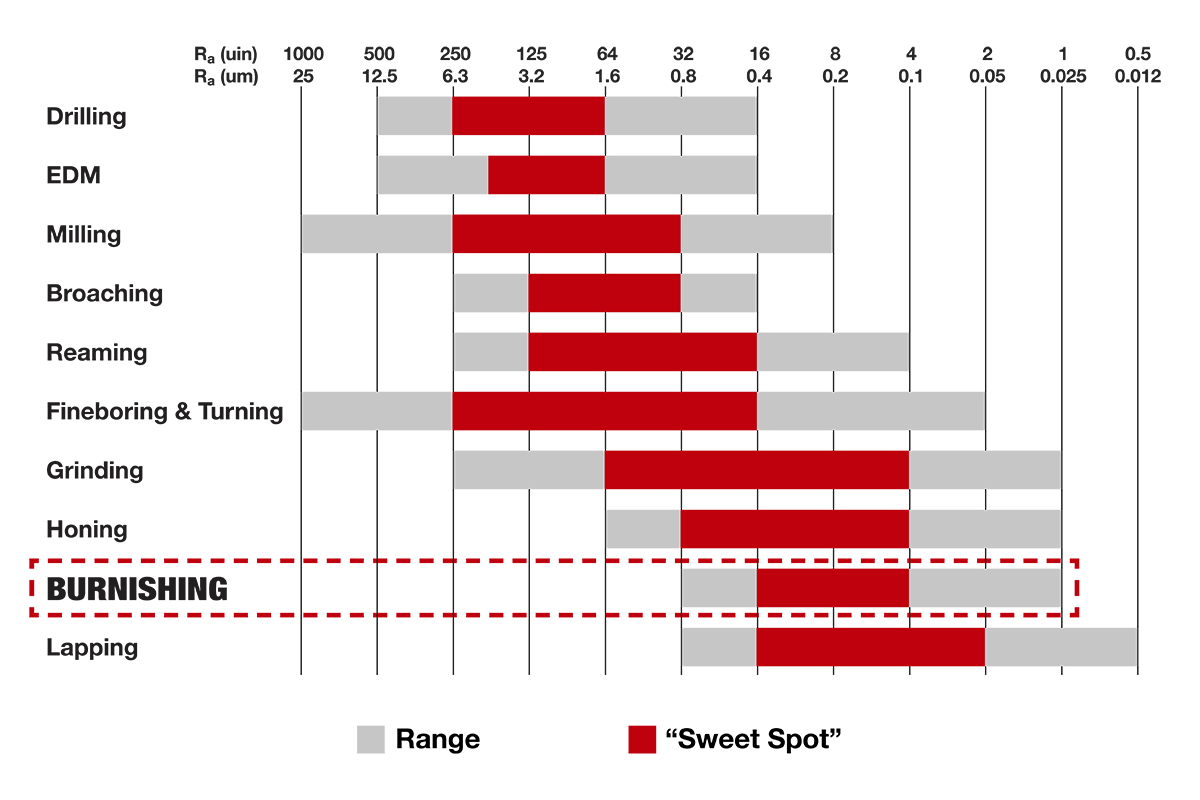
Traditional Finishing Methods
When talking about surface finishing processes, there are several specialized processes that have been around for a very long time. Grinding, Lapping, and Honing are some of the most common methods when trying to produce a smooth surface finish. As it sounds, grinding is the process of shaping the outer surface of a part using a grinding wheel. The benefit of grinding is that it’s simple to do, however, there are limits on the shape and size of the part that can be run. Since this process relies on a central axis of rotation it only works with cylindrical surfaces. Additionally, the smaller the part, the more challenging it is to set-up correctly, making it more effective on larger surfaces.
Lapping is another common method of metal surface finishing and is a process where two surfaces are rubbed together with a loose abrasive between them. Generally used on flat surfaces, lapping has the ability to produce a very fine surface finish. Lastly, honing is a process that sizes and finishes the interior of bores or tubing. This is typically done with honing stones and follows grinding, boring, and drilling operations. While lapping and honing produce high quality results, they are incredibly tedious and time consuming processes. Additionally, due to the specialized equipment required, many customers end up having to outsource parts which can add cost and lead time.
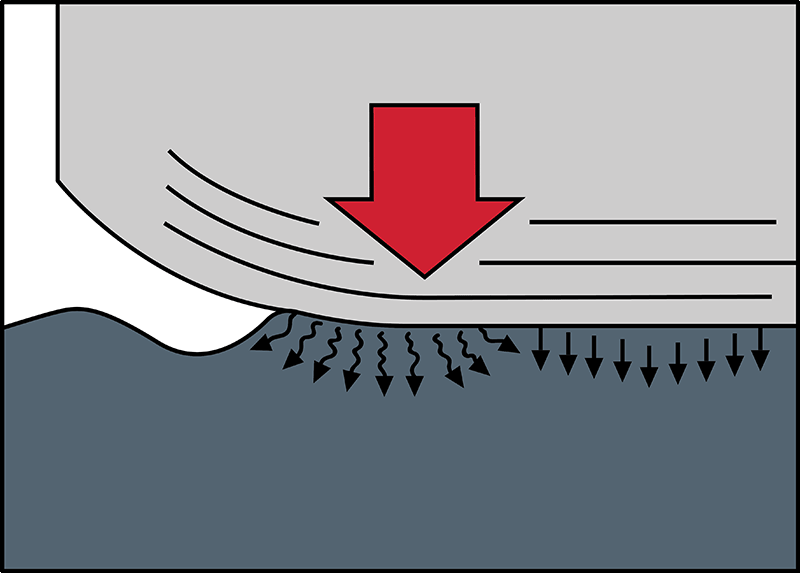
Burnishing
While traditional finishing methods are effective, they are not very efficient. In many cases, these processes require multiple operations and set-ups to achieve the desired finish and results. This means there’s a lot of cost and downtime to change over parts. Additionally, more specialized processes like lapping and honing often require an outside vendor which adds cost and lead-time to manufacturing. Many shops are looking for ways to reduce the number of operations required to save on cost, as well as increase production. Burnishing is an effective and efficient alternative that often eliminates the need for secondary processes entirely.
Burnishing is a machining process that cold works the metal without removing material. Rather it compresses or “irons-out” the peaks of a metal surface into the valleys, resulting in a uniform surface. Depending on the application, a burnishing tool uses either 1 or multiple rolls to exert pressure on the workpiece. This condenses the grain structure of the metal and causes it to elastically deform until it achieves a smooth surface finish.
In addition to creating a smooth finish, burnishing also increases the material’s resistance to wear by work hardening the surface of the workpiece. This results in better part life, as well as, better abrasion and in some cases corrosion resistance.
In general, most ductile metals can be burnished and achieve a low finish. This includes stainless steel, titanium, aluminum, Inconel, etc. The ending finish will depend on the material and starting finish of the part. To read more about materials and surface finish, visit this article.
Overall, there are many different existing methods for surface finishing. grinding, lapping, and honing are some of the most common methods used today to achieve finer finishes. While these methods can produce a high-quality finish, they are often high cost and outsourced to a vendor who has specialized equipment. In order to achieve the same fine finishes in house without secondary operations, many shops are turning towards burnishing applications. This allows customers to achieve specified finishes in one machining operation, saving time and money.
Browse our full line of Burnishing Tools to find the perfect solution to streamline your manufacturing process.
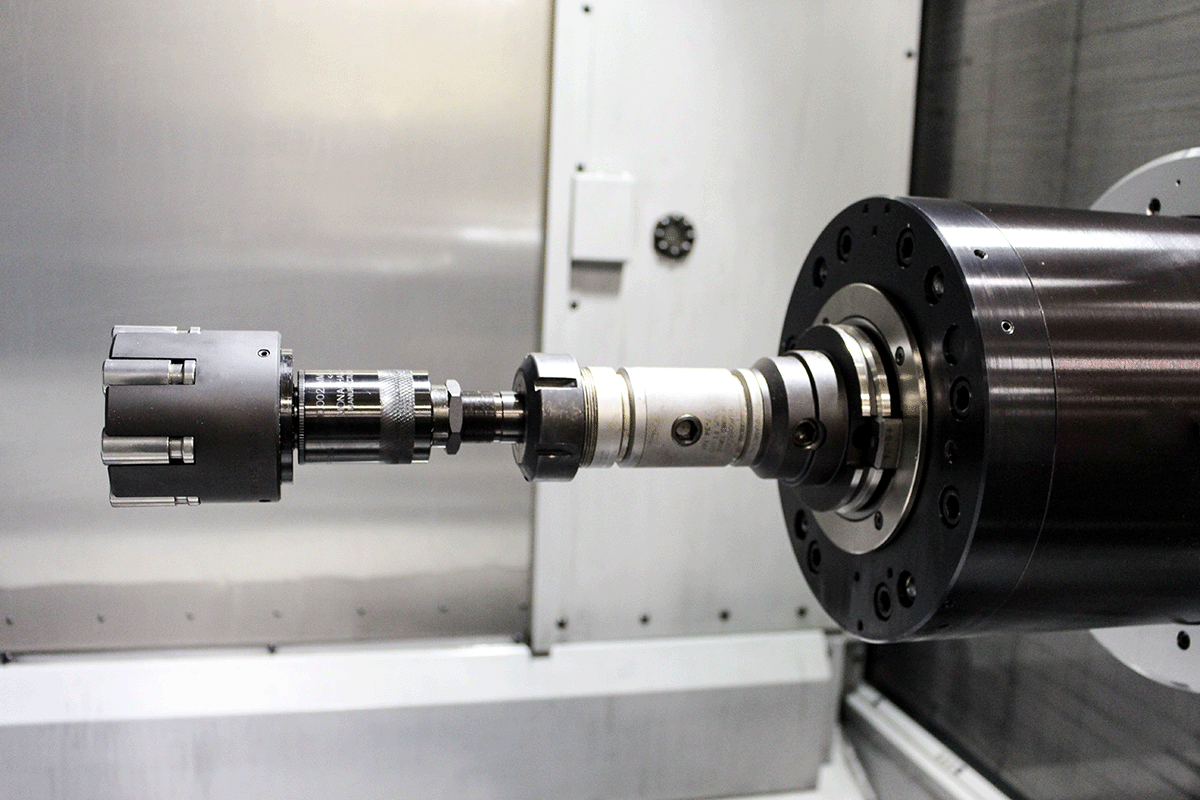
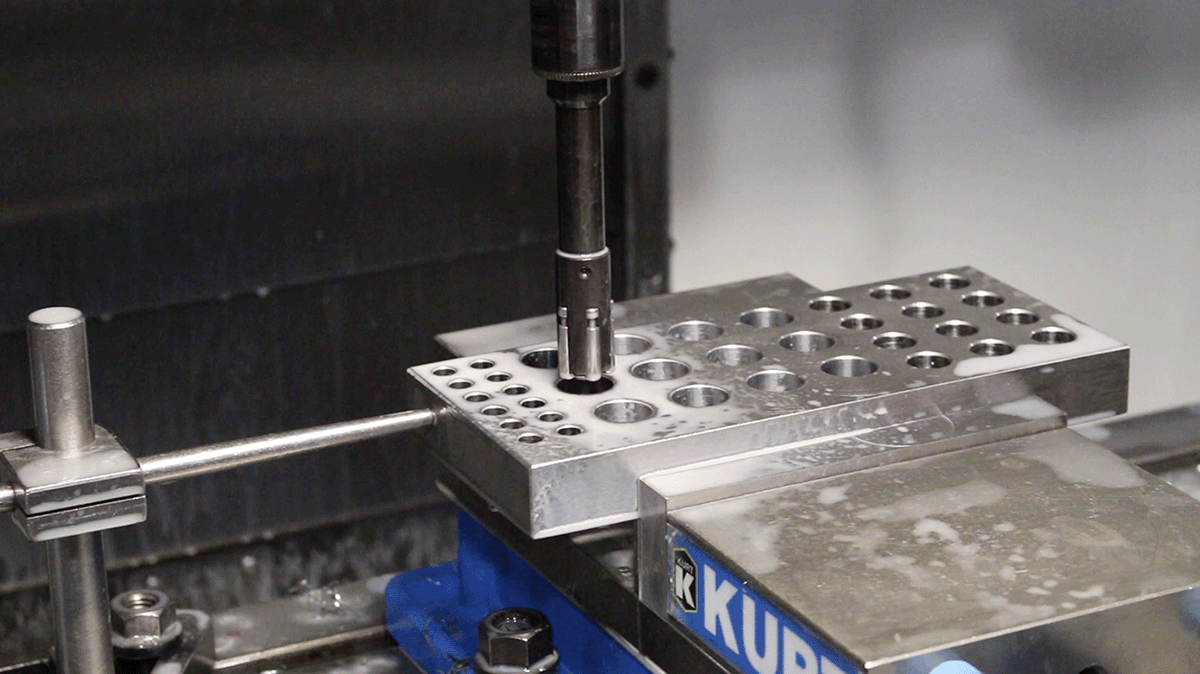