How Material Impacts Surface Finish
In manufacturing, there are many processes that can impact the performance of a part. From the design itself to the machining method used, there are many variables at play. One critical step in this process is the ending surface finish of the part. Not only does surface finish impact the aesthetics of the part, but it also plays a large role in part performance and efficiency. While there are many finishing methods available, this article will focus on burnishing and how different materials will impact the surface finish of the part.
What is Surface Finish?
Surface finish is the measurement of a material’s texture and is made up of three key parts: lay, waviness, and roughness.
- Lay describes the direction of the surface pattern on the material and is generally a result of the manufacturing process used.
- Waviness refers to large irregularities or deviations on the surface of the material
- Roughness, like waviness, evaluates smaller irregularities in material and is used to calculate its smoothness
Depending on the end use of the part, the acceptable range for surface finish will vary, however, most machined workpieces will require a lower finish. For example, mating surfaces or parts that will interact with others while in operation will utilize a lower finish to help reduce friction and increase efficiency of the part. Burnishing can also improve corrosion resistance and part life due to surface hardening.
Units of Measurement
The most common units of measurements for material roughness are Ra and Rz. Ra refers to the average roughness of a material, where Rz refers to an average vertical distance of the highest peak and lowest valley. Ra is most used in the United States and Rz is used internationally. In both cases, a lower number (ie. 16) indicates a finer finish where a higher number (ie. 80 – 100) indicates a rougher finish.
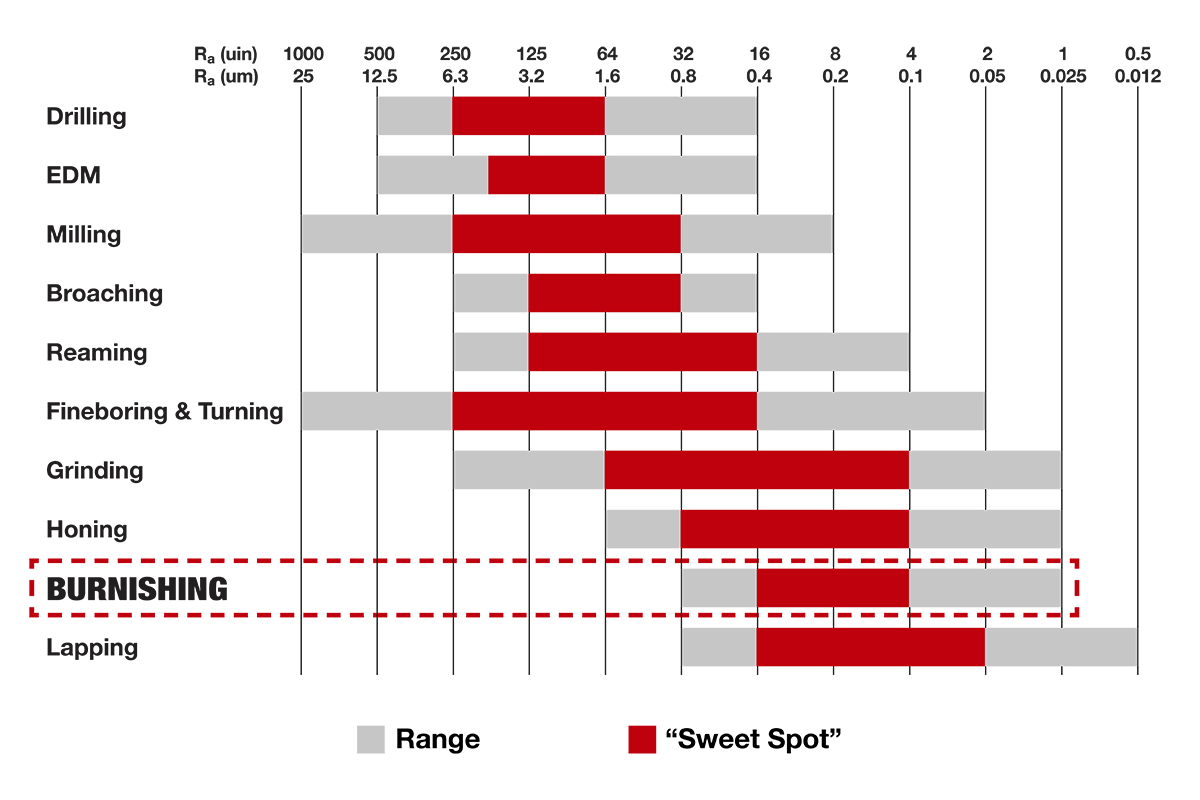
Materials and Surface Finish
The ending surface finish of a part will depend on a few different factors, the first being the material itself. When it comes to burnishing, not all materials will behave the same way. Ductility refers to a materials ability to bend or deform before breaking. Since burnishing uses compressive forces to iron out the peaks and valleys of a material, the material must be ductile. The hardness of the material will determine the achievable final finish. In general, ductile materials will respond better and be more capable of achieving a finer finish compared to hardened materials.
Common Ductile Materials |
---|
Aluminum |
Brass |
Inconel |
Stainless Steel |
Steel |
Titanium |
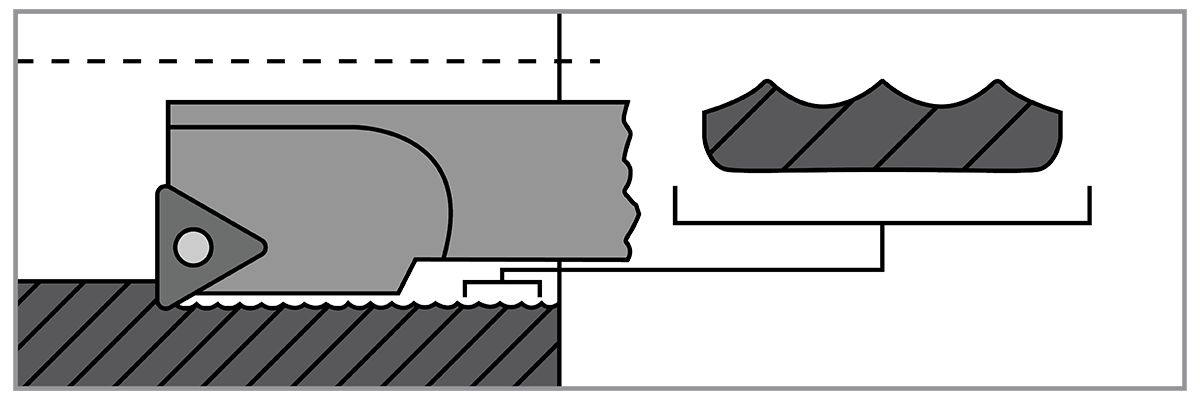
Surface Preparation
To get the best finish, it’s important that the surface of the material is prepared appropriately. Burnishing requires a prominent peak and valley pattern to get a finer finish, because it provides more surface area for the material to be moved. As a result, it’s important that softer materials start with a coarser finish, such as 80 – 125 Ra, to allow the burnishing tool to work correctly.
When working with less ductile materials, a finer machined finish will be required before the burnishing operation to reduce the amount of material that needs to be moved during the process. Regardless of the material, gouges and tears in the surface caused by drilling, reaming, or turning will be difficult to remove during the burnishing process. As a result, they will likely remain visible after the burnishing operation is completed.
Once the surface has been prepped accordingly, the burnishing operation can begin. In high ductile materials, lower “mirror” finishes such as 4 Ra are possible. In harder materials, a finish of 16 Ra will often be the most common target. Generally, it’s recommended that a few test pieces are set up and run to determine the right pressure and feed rate required to achieve the desired finish.
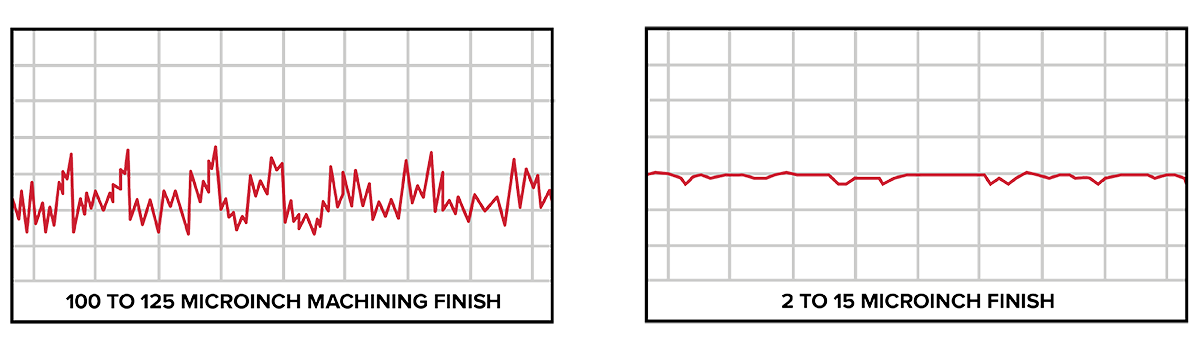
Overall, surface finish plays a critical role in determining the performance and longevity of a part. Finer finishes are often used to improve mating surfaces and reduce friction in rotating pieces. One of the easiest methods to achieve a low surface finish is through burnishing, as it is an easy one step operation. However, it’s important to understand what materials can be burnished and how material impacts the finish that can be achieved. With this in mind, operators will be able to determine the steps required to prepare the part for burnishing, as well as the optimal feeds and speeds required to achieve the desired finish.