How To Size An Expander For Center Tube Sheet Expansion
The design of a chiller can pose some challenges when it comes to tube installation and maintenance. From the center tube sheet to tube enhancements, special considerations need to be made when choosing the correct tooling for the job.

Due to the design of the vessel, customers are required to expand tubes into a center tube sheet. This separates the evaporator from the condenser, allowing it to function properly while in production. The most common method for expansion is with the use of a long reach expander, however, it can pose some challenges. This is largely due to the long reach required to get to the center tube sheet. Generally, most chillers have about 10 – 15 ft of space from the front of the vessel to the center, resulting in custom tooling and a challenging set up. Additionally, chillers are often made with enhanced tubing, meaning there is a pattern or form created in the surface of the tube to aid in heat transfer. These enhancements can make sizing tooling for the job more complicated, as the ID of the enhanced portion of the tube is smaller than the ID of the prime surface where the tube is rolled.
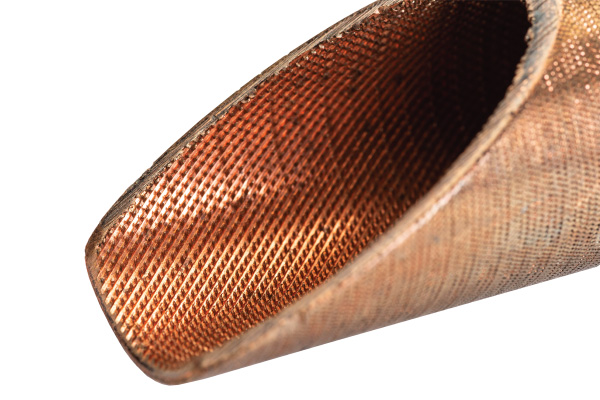
Micro Deformation Enhanced Tube
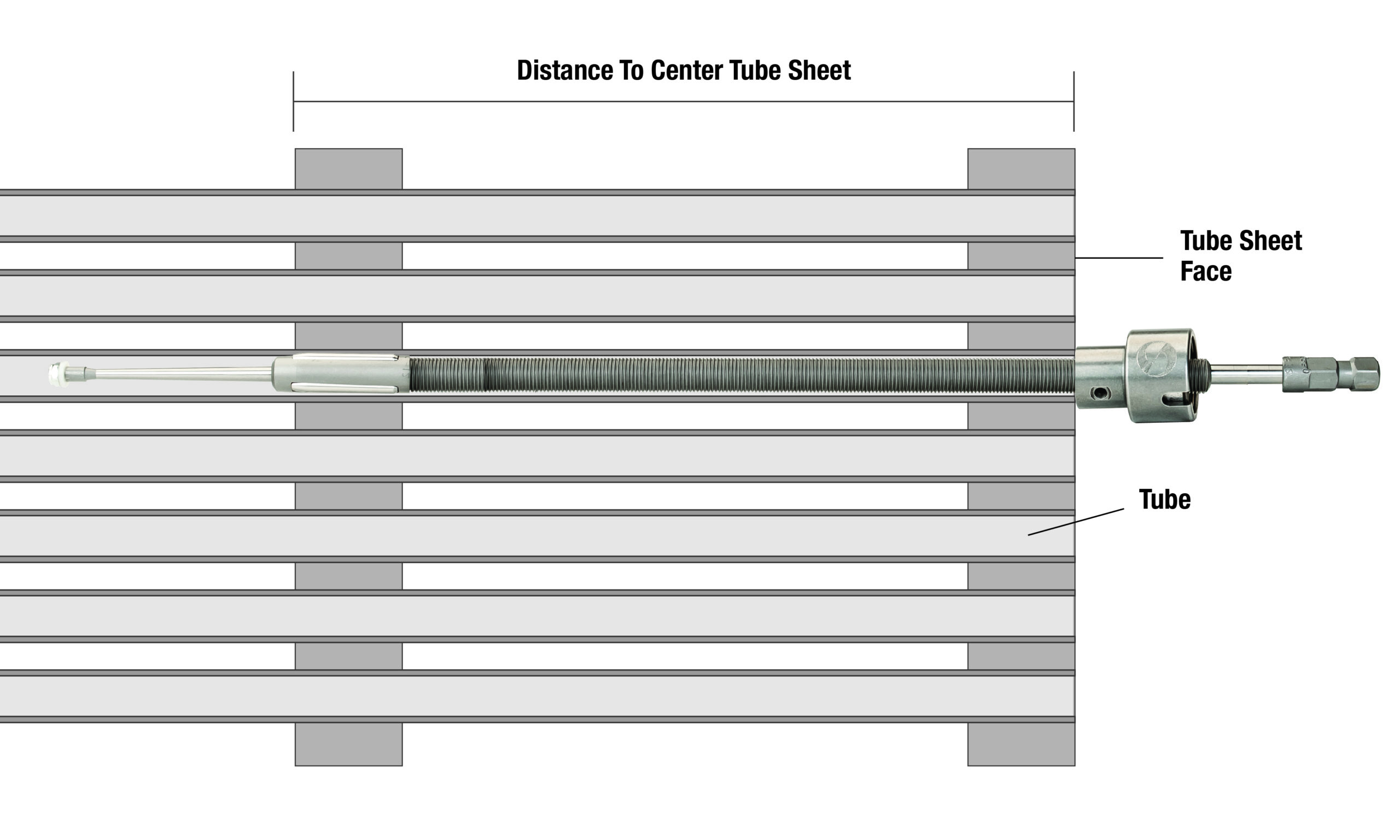
Before selecting a tool there are a few measurements that will need to be provided. First, the distance from the front of the tube sheet to the center tube sheet. It’s also important to note where that measurement falls- for example, is it to the back of the center tube sheet or the center. This will help in determining the required overall reach of the tool. Second, the ID of both the enhanced portion of the tube and the prime portion of the tube. Since the enhanced portion is often smaller in diameter, the cage of the expander will need to be designed to fit through the tube and maintain the necessary expansion range to hit the desired wall reduction. Lastly, the center tube sheet thickness will help determine what roll type and length will be needed for the expander.
Once you have all this information, a long reach baffle expander can be made to your custom application. When expanding the center tube sheet, it is critical that the tool be held perpendicular to the tube sheet. If the tool is not straight or an operator leans on it, it can cause the tool to break, or the motor may produce a false torque reading. This can result in more money on tooling and potential for the tube to come loose from the tube sheet. Additionally, before rolling, the collar should be adjusted so that the rolls are in the center tube sheet. If the collar is not set correctly, it can result in rolling in front or behind the tube sheet, damaging the tube enhancements. The easiest way to find the right spot is by using a drawing or measuring off the distance.
Overall, expanding the center tube sheet can take a lot of prep work and time to execute correctly. However, once it’s set up, it’s a fairly easy operation. To make sure you get the right sized expander for the job, you’ll need to calculate the distance from the front of the tube sheet to the center, measure the prime and enhanced tube ID, and measure the thickness of the center tube sheet. With the right sized tool in hand, you’ll be able to create a good mechanical seal and prevent tube leaks over time.