What Makes A Quality Air Motor?
The quality of an air motor will be determined based on manufacturing processes, design, and maintenance. In order to improve cleaning performance and tool life, it is important that the motor is designed for use in a specific application. This assures optimum performance and extended life of the motor.
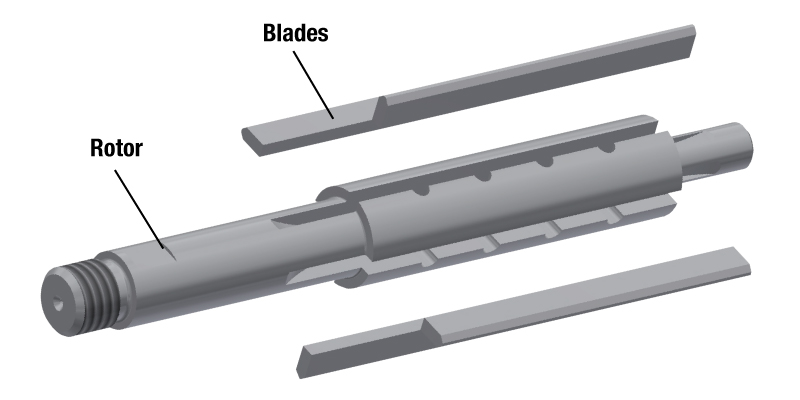
A turbine style air motor is a type of rotary vane motor. As pressurized air enters the body of the motor, it expands against the blades or vanes, turning the rotor. The motor generates power by converting the air pressure on the vane to a turning force (torque). Torque is then transferred from the vanes to the rotor, and ultimately to the cutting head attached to the tool.
Manufacturing Processes
Components such as the motor case, cylinder, rotor, vanes, thrust plates, bearings, etc, have varying manufacturing processes to provide the best wear and durability of the part. Tolerances and material will both influence the performance and life of the motor.
Maintaining Tight Tolerances
One of the most important considerations when manufacturing an air motor is the tolerance. Since no machine can produce something to a specific value every time, an acceptable amount of variation must be determined. If a part exceeds a specific tolerance, then it is no longer usable for that specific design.
In air motors, the tighter the tolerance the more efficient the motor will be. If there is too much space between parts, the horsepower of the motor will decrease. On the other hand, if the tolerances are too tight, it will increase cost and take more processing time. Therefore, it’s important to find an acceptable range that produces enough horsepower for the application but isn’t cost prohibitive.
Material Selection
The materials used for the different component parts will largely be determined based on their mechanical properties, such as hardness and toughness.
Hardness is a materials ability to resist scratches and abrasions. This will determine how a part will wear over time.
Toughness is a materials ability to resist cracking when force is applied. This allows a material to absorb this force before breaking.
Each motor component is made with a different material to help control wear and durability. For example, the motor case needs toughness so it doesn’t crack while in use, but it also needs hardness to be durable and resist scratching.
Optimizing The Motor Design
The cleaning application will determine the size and length of the motor. For example, in curved tube applications the motor needs to be short enough to navigate the bend in the tube without sacrificing power or torque.
In general, the longer the motor, the more power or torque it has. However, at some point it doesn’t make sense to keep extending the length of a motor, because at a given length it maximizes the power needed for the application. Instead, it’s more important to optimize the components inside of the necessary motor diameter. The tighter the components fit inside of the motor, the more power or torque it has.
Motor Wear
One of the most common issues that occur with air motors is the wear of thrust plates, bearings, and vanes. When a motor is running at high speeds, parts will begin to wear over time. Eventually, the motor case itself will wear, but not as quickly as the internal components.
It’s important to change out wear parts at the first sign of motor efficiency loss. When this occurs, it means the paddles aren’t extending like they should and they’re wearing down. Once the wear reaches a certain threshold, power or torque will be reduced.
When operating a turbine motor it’s important to lubricate the air source to keep the motor from overheating. It’s also necessary to maintain a consistent air supply to the motor because it will give the motor more consistent power or torque. If there isn’t enough air, the motor can lose power or torque and provide an inadequate clean.
Overall, air motors should be manufactured to a suit a specific application, in order to provide the best cleaning performance. Manufacturing tolerances, materials, and design principles can all impact the quality and performance of an air motor. In order to maintain cleaning performance and extend tool life, it is critical that motors are well maintained and operated properly.