Elliott offers the 445 Series Motors in both roll and lever throttle for tube sizes 2.000” (50.8mm) to 4.000” (101.6mm) to suit your tube expansion needs. The powerful 445 Series Motors are ideal for tough boiler tube applications. The right angle heads are suited for rolling tubes in hard to reach, tight areas.
Upon delivery of the 445 Series Right Angle Rolling Motor, read and save all instructions. Before use, be sure everyone that will operate this tool reads and understands the instructions and technical manual, as well as any labels packaged with or attached to the tool.
The Right Angle Rolling Motor is designed to operate on 90 PSI (6.2 bar) air pressure using a 1/2” hose up to 8 ft. in length. The in-line lubricator should be checked and filled regularly with a good grade of 10W machine oil. The motor requires the air supply to be clean and lubricated with an “in-line” or “wall mount” filter/lubricator and set to dispense the recommended lubrication quantity. Always use an air line lubricator when operating even for a very short time.
There are two models available, a roll throttle style and lever throttle style. The lever style is activated by simply pressing down the lever and is de-activated by releasing the lever. For the roll throttle style, simply rotate the handle in either direction.
Lever Throttle
Roll Throttle
Always use the Torque Reaction Bar when operating these tools. Never brace the aluminum handle or the Torque Reaction Bar of the tool against anything to absorb the torque of the tube rolling or tube cutting operation. If this is done, damage to the handle or Right Angle Head connection to the handle can occur.
Always use the “pin” or tighten the set screw of the Square Drive Chuck when operating the motor. Under rolling load, the square drive of the motor can “back out” of the Drive Chuck.
While using the motor, if the torque control stops as soon as the throttle is engaged, the torque setting on the motor is set too low. Increase the torque setting value to reset the Torque Sensor. To do this, when motor is not running, rotate the adjustment cover until the adjustment slot is uncovered. With the angle head end to the tool facing away, use a 5/32” diameter pin to rotate the adjusting nut clockwise to increase the torque setting and counterclockwise to decrease the setting. After adjustment, rotate the cover over the slot to lock the nut in place. The direction in which to rotate adjusting nut is marked on the cover for reference. After adjusting the torque and before operating the tool, be sure to grip tool securely and be prepared to counteract stall torque in case clutch is improperly adjusted.
If the clutch is adjusted over the maximum power output of the tool, the clutch will not function and the tool will operate like a stall-type tool. Also, if the tool is being operated at its upper torque limits, a drop in air pressure could cause the clutch not to function due to a loss of motor power and the tool will function like a stall-type tool. If the motor has stalled due to over adjustment of clutch, release throttle and do not try to continue using motor by rotating it manual (as if it were a ratchet-type tool). This will break the rotor paddles and could also damage the cylinder.
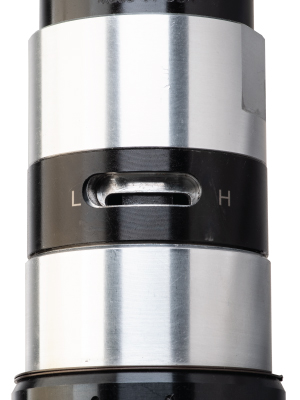
NOTE: Do not set the motor at full torque. It is important to back off at least two clicks to allow the motor to run down.
For more information on the 445 Series Right Angle Rolling Motors, visit our webpage or contact Elliott.