Overcoming Challenges with Expanding Small Tubes
Tube expansion can be challenging regardless of the application. From inconsistent wall thicknesses to exotic materials, a lot of factors can influence the quality of an expansion. In smaller applications, there can be some additional complexity to the process which makes choosing the right expander more critical.
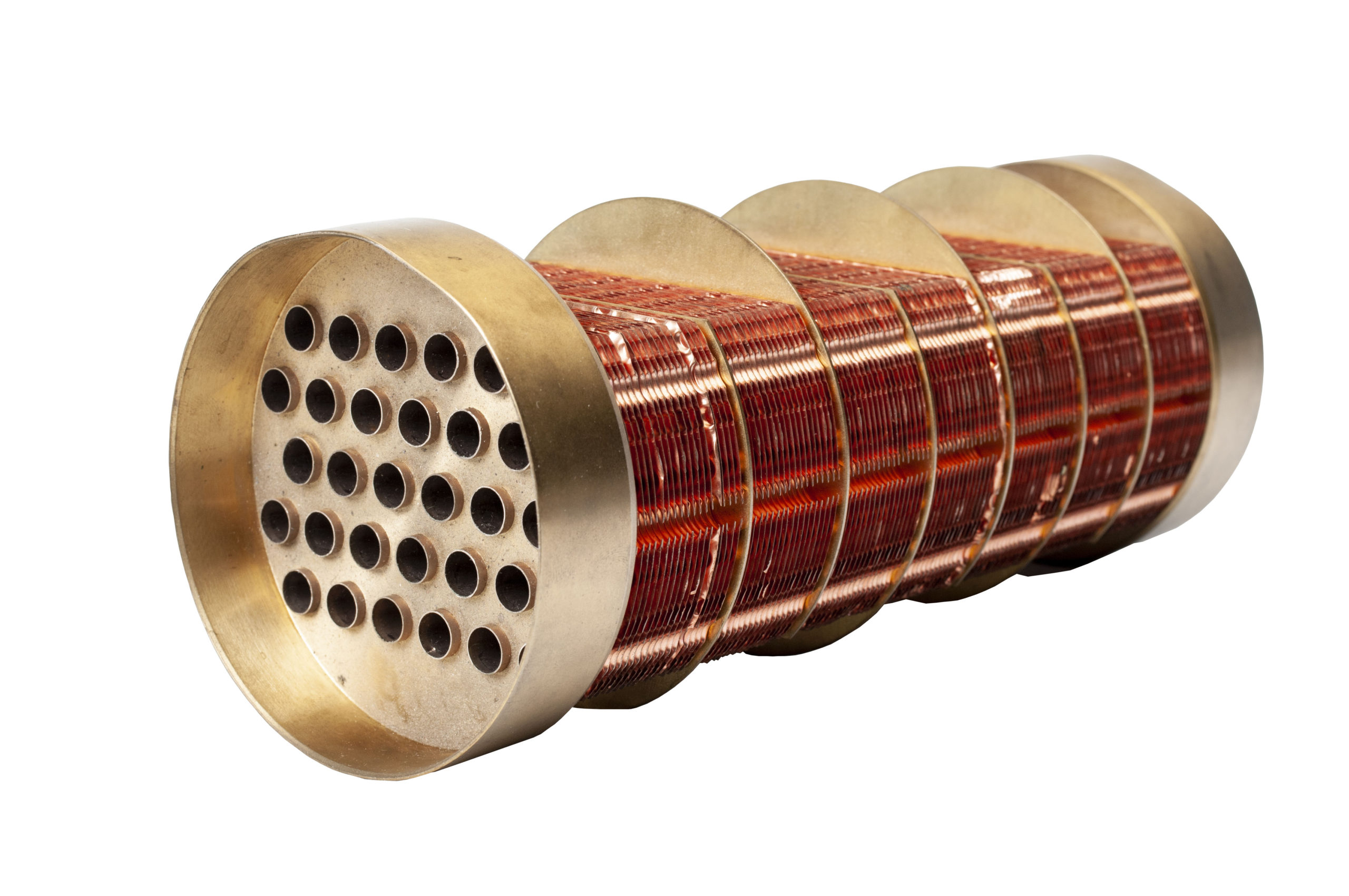
What Are Small Heat Exchangers?
In general, small tubes tend to range from ¼” – 3/8” in size and are found in small heat exchangers or oil coolers. The smaller size makes these ideal for use in more unique applications, such as submarines, jet engines, or convenience stores. Depending on the industry, these vessels can have more restrictions or limitations on what can be used during the expansion process. For example, lubrication can be a big issue in certain applications where residues cannot be left behind, making heat reduction and tool life a challenge.
Tool Life & Maintenance
As tooling gets smaller, there are more concerns around prolonging tool life and performance. This is because the surface area of the tool has decreased, increasing friction. In cases where lubricant cannot be used, operators will notice a lot more premature wear from heat build-up. If lubricant can be used, it is highly recommended in order to extend the life of the tool.
Regardless of lubrication used, small expanders will require more preventative maintenance. In larger expanders, the cage has ample room for debris to naturally flush itself out. However, as the cage gets smaller, the amount of space for debris is limited. This can result in more buildup of tube material deposit or lubricant inside of the expander. One of the easiest methods for cleaning out an expander is with an ultra-sonic cleaner. Generally, tooling should be cleaned after every 50-70 expansions, but can vary depending on tube material. To reduce downtime due to cleaning, it can be beneficial to have two expanders ready to go so they can be swapped out for cleaning.
Overall, if you can keep your expander clean and cool, it will perform better and last longer on the job.
Expansion Process
When working with smaller tubes, it is critical that the right sized tool is selected for the job and that a consistent wall reduction is maintained. As tubes get smaller, so does the wall thickness and ligament distance between tubes. This difference in size can make it easier to get an out of round tube or to over-roll a vessel. Both of which can ultimately result in leaks and damage the tube sheet.

Tenting or Uneven Expansion
During the tube expansion process, the rolls push against the inside of the tube allowing it to expand against the tube sheet hole. Each time a roll passes a specific location on the ID, the force creates a stress in the metal. Depending upon the material, the tube may try to resist the force being applied and return to its initial state. The more the expander works the tube material, the faster the tube will work harden, meaning it is no longer malleable.
Tubes with thinner walls are more prone to work hardening due to the thinness of the material. If the expander is not sized correctly it could result in an uneven roll, known as “tenting”. In larger sized tubes, one of the best ways to prevent tenting is with a 4 or 5 roll expander. However, smaller tools don’t always allow for modifications due to the limited working area.
One of the best ways to prevent tenting in these applications is to ensure that the expander is sized to the tube ID and that the right motor is being used. Less force is required when rolling thin-walled tubes, so the fastest setting on a low torque will allow the tube to be rolled quickly enough to prevent tenting from occurring. For example, a 24 BWG copper tube could be rolled with a 2,500 RPM motor on the lowest torque setting.
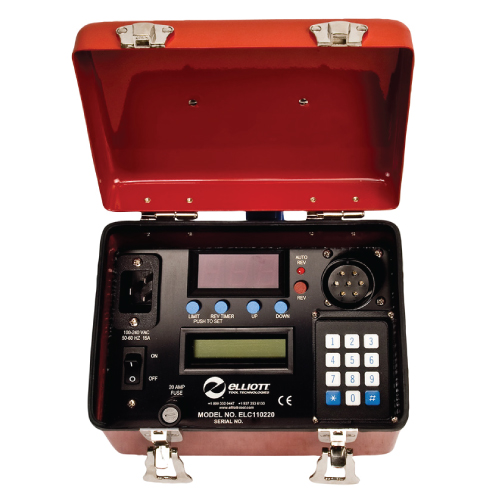
Over-Rolling Tubes
Tubes are considered over-rolled when the expansion of the tube surpasses the expansion required for the proper wall reduction. Over-rolling can decrease the distance and strength of the ligaments between tubes, causing considerable damage to the tube sheet and tubes. Once a ligament is weakened, it will reduce the strength of those around it, causing adjacent tubes to leak.
Over-rolling is one of the most common challenges faced with smaller tubes due to closeness of the tube sheet holes. As a result, even the slightest bit of over-rolling can result in leaks and deform the tube sheet. Once a tube is over-rolled, there isn’t a lot that can be done to correct the issue and can result in additional rework and maintenance costs. To avoid over-rolling, it’s important to get an accurate tube OD and ID measurement prior to expansion so the proper wall reduction can be calculated.
Once you know your target wall reduction, you’ll need to maintain that expansion percent throughout the entire tube bundle. One of the best ways to ensure this is to use a torque controlled rolling motor. Torque control options are available for both electric and pneumatic motors to allow for different variables. Pneumatic is the easiest to use and can be set by adjusting the tension on the torque spring. However, both options will depend on the customers’ access to air and power where they are working.
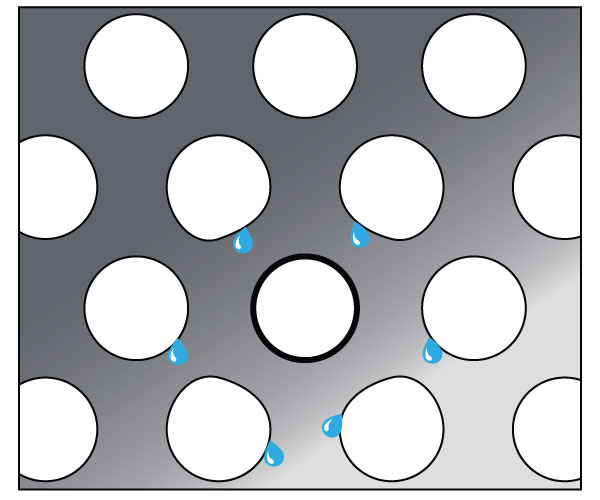
Overall, expanding small tubes can be challenging if certain factors are not considered. Understanding expander care and maintenance will go a long way in preserving tool life and performance. Additionally, selecting the correct expander size and motor will help prevent uneven rolling or tenting in thin wall tubes. Lastly, calculating the correct wall reduction percent and controlling the amount of expansion using a torque controlled motor will reduce the need for rework from over-rolled tubes.
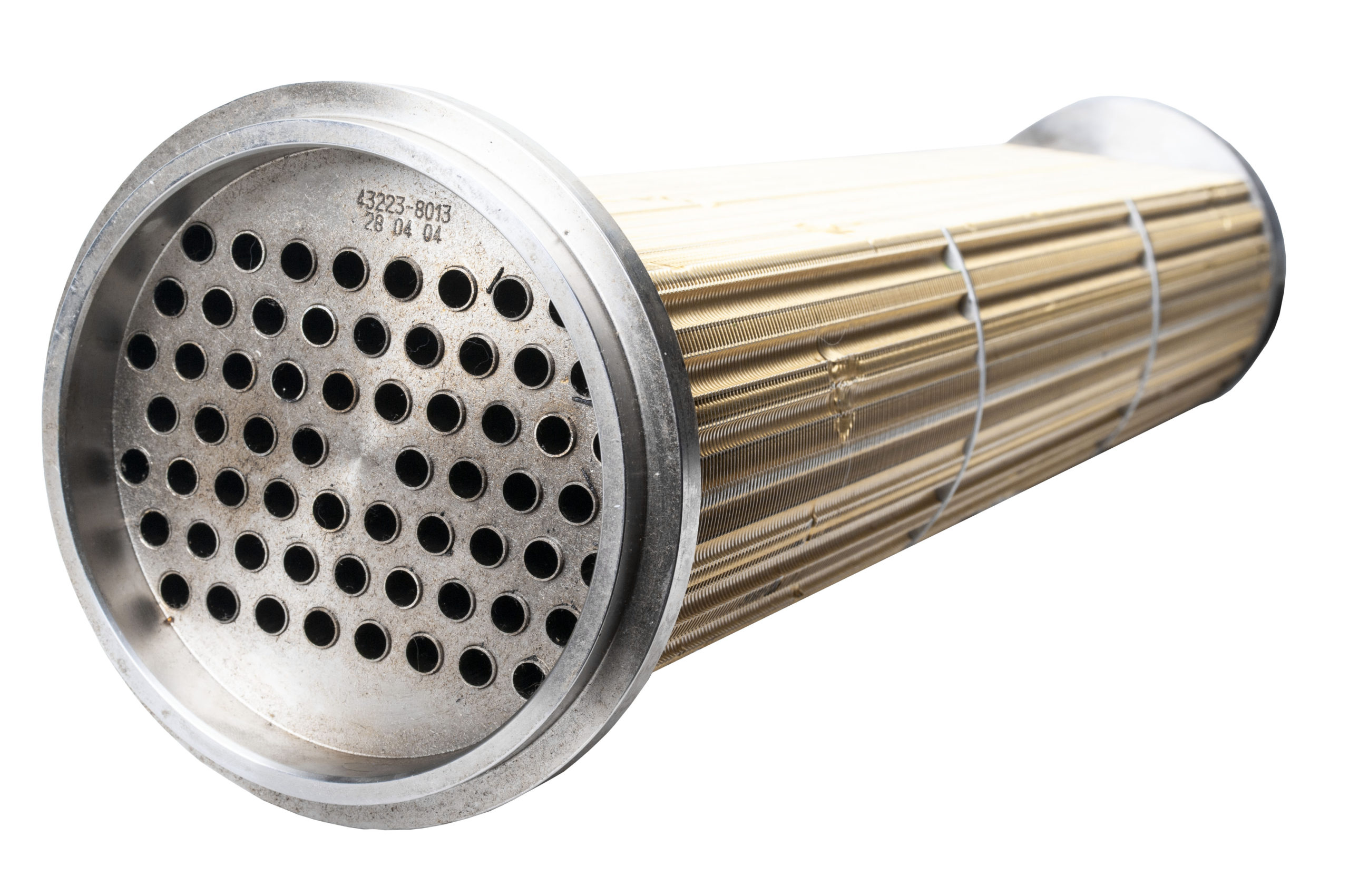