Mitigating Glitch on Shafts Using Diamond Burnishing Tool
Diamond burnishing tools can be used to help mitigate electrical and mechanical runout (glitch) on shafts.
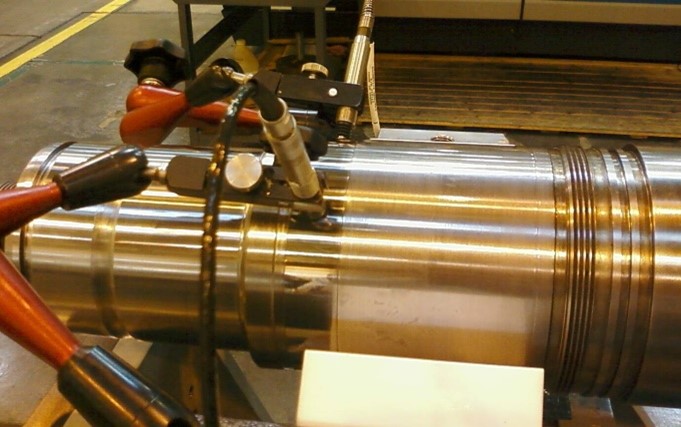
Runout
Rotors or shafts used in steam and gas turbines, turbo generators and compressors, or any large motor, have to work within set standards for runout to ensure efficient and safe operation.
Mechanical runout can be measured using a Dial Test Indicator (DTI) to establish the dimensional error as the shaft is rotated through 360º. Factors affecting this include the quality of the turning machine, the tooling being used, the grinding process, and material handling.
Electrical runout is the apparent displacement of a rotating shaft. This is measured with proximity probes (eddy current sensors). The unwanted shaft movement is caused by variations in the shaft materials electrical and magnetic properties. Factors affecting this will include the material composition, how the shaft is forged, heat treatment, grinding techniques, induced magnetism, stress, and material handling.
If excessive runout is not eliminated during the manufacturing process, the motor would have to be disassembled and the shaft reworked. This can be a time consuming and costly process and one the motor manufacturer would want to avoid.
Diamond Burnishing
So how does the use of a diamond burnishing tool help reduce the Glitch or electrical runout of the shaft?
Burnishing is a technique in which the surface profile of the material is displaced, in this case with a diamond knib, with the process for this application normally being carried out on a turning machine.
The diamond knib is mounted in a tool holder with an adjustable spring pressure, and is used to apply a load as the knib is fed along the length of the journal track. The burnishing process induces plastic deformation in the top layer of the material, altering the crystal structure, and produces a high-quality surface finish typically under 0.3µm Ra (12µ” Ra).
The induced change realigns the surface structure of the material matrix resulting in a reduction in the electrical runout of the shaft, which in turn will lead to reduced vibration and noise when the shaft is in use.
This API (American Petroleum Institute) recommended method has a high success rate of reducing “glitch” to within acceptable limits as it produces a uniform work-hardened surface requiring no further treatment.
The technique can also be applied when repairing worn shafts as the burnishing process can help to eliminate the effects of surface damage due to mishandling and wear.
Elliott Tool Technologies has been a supplier of Diamond Burnishing tools for this process for many decades, with tools being used across the globe. The premium quality of the diamond knib ensures repeatable results for the end user.
Have specific questions about the Diamond Burnishing Tool or an upcoming job? Contact our application specialists.
