Installing Mechanical Tube Plugs
When needing to use and install mechanical tube plugs, having the correct tools for the job can make it easier and quicker to get the job done. Below are step by step instructions to help overcome this challenge.
Clean & Prep
Prior to any work being done it is important to brush the tube using Elliott’s MPB brush sized properly for the tube ID. The MPB brush is a rigid steel wire brush that is designed to remove material from the tube to create a prime surface that the plug can seal against. The brush can be driven by a standard handheld drill. If the MPB brushes does not create a prime surface, an adjustable reamer can be used.
Please note the size and use caution to not over adjust the reamer and remove too much tube wall during this process. Elliott suggests that the adjustable reamer be driven by hand power only to avoid damage and control the reaming.
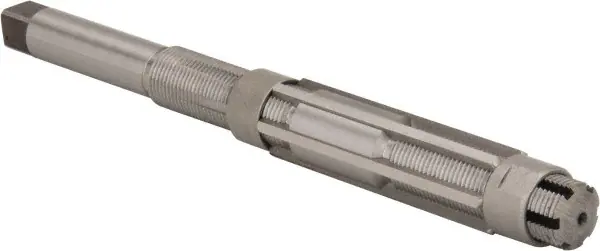
Adjustable Reamer, Image provided by MSC
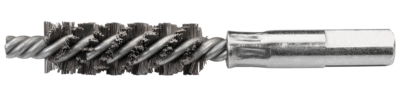
Mechanical Plug Prep Brush
Measuring
Elliott’s Tube Hole Gauge can be ordered for a wide range of sizes and reaches to overcome any reach constraints. When using this tool, it is important to measure in the area that you plan to install the tube plug and ensure that after each measurement, rotate the gauge 5-10° to further check the tube for any tenting or irregular shapes. Be sure to log this information so that it can be tracked for quality assurance.
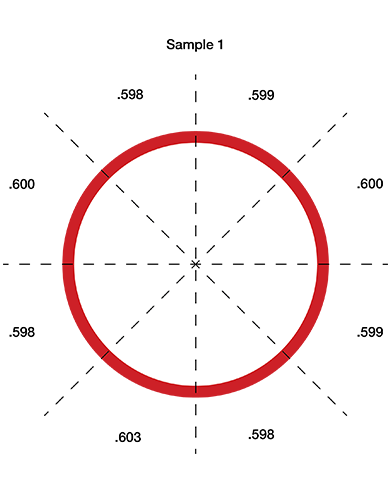
Tube ID Irregularities
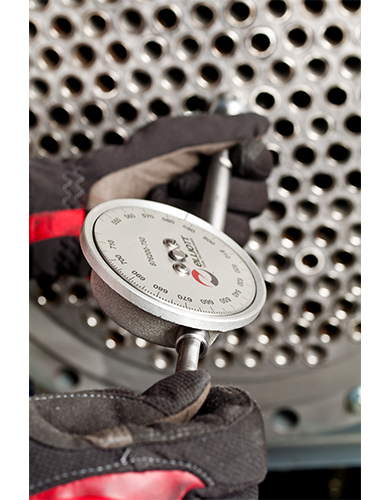
Tube Hole Gauge
Venting
One of the most overlooked best practices for plugging a tube is to vent the tube beforehand. Tube venting is a process by which a small puncture is made inside of the tube, releasing any pressure or chemicals that may be trapped inside. Venting is highly recommended for oil refineries, petrochemical, chemical and other processes that utilize heat exchangers and feed water heaters. Certain chiller applications may specify otherwise, so it’s best to check with your manufacturer.
To do this, we recommend using Elliott’s One-Rev tube cutter. The vent should be beyond the tube sheet to ensure the tube does not build up pressure and create risk for plug dislodging, fire, or explosion. Venting can be done on both ends of the tube, as well as, on the top and bottom of the tube. This ensures that pressure cannot build-up later on due to corrosion or process fluids.
- Determine how far down the tube you wish to make the cut and lock the collar in place.
- Insert the cutter into the tube and start rotating the cutter clockwise.
- When you begin to feel some resistance, rotate the tool a quarter turn more to pierce the tube.
- Turn the cutter counter-clockwise to reset the cutter bit. Once the bit is retracted, the cutter can be removed.

One-Rev Tube Cutter
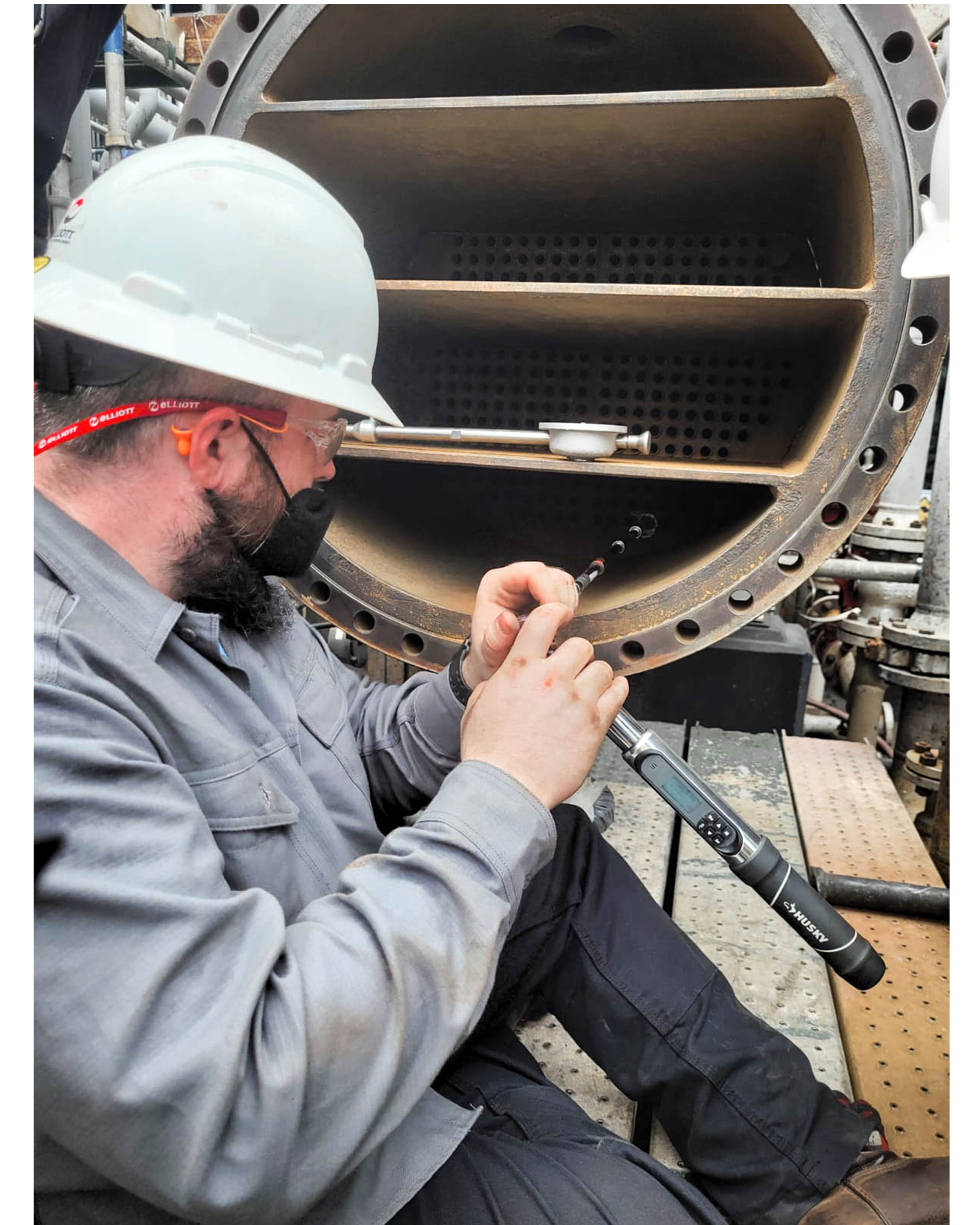
Tube Plugging
Once the above has been completed, the operator can now choose the correct plug for the tube and application. Remember it’s important to match like materials and to select the appropriately sized plug for the tube ID being plugged.
During installation you may find that you need accessories to reach through channels for water boxes. This will be dependent on the vessel and space constraints. Things to keep in mind:
- If using socket extensions, be aware that extreme reaches could result in slight loss in torque. Double check the torque value on a test stand to anticipate and account for any loses.
- Brush extension kits are available from Elliott to ensure you can reach through headers, water boxes, and channels to clean the tube end.
- Air coolers pose a unique challenge as a 12’ reach expander could be needed to expand the tube past the tube sheet so that the eccentric cam has room to lock into place during installation.
To install the plug, select the correct size and place the plug on the end of the provided hex key until you hear a slight ‘snap’. This indicates that the plug is secure. When positioning the plug, be sure that the serrated portion of the plug lands within the tube sheet area. This will ensure that the plug seals against the tube and tube sheet to allow for optimal performance. If the serrated area lands outside of the tube sheet area, the plug and torque wrench could reach torque but during testing and operation, the plug could come lose and leaks would be present.
Once the plug is placed in the appropriate spot, take your torque wrench and start turning until torque increases. Elliott recommends the use of a digital torque wrench that features color, audio, and vibration alerts when you meet your desired torque. Once you reach the desired torque, stop applying force and remove the hex key from the plug and repeat this process for the next tube.
If you feel you have a more challenging application and wish to discuss, please contact us at sales@elliott-tool.com and ask for an application specialist.