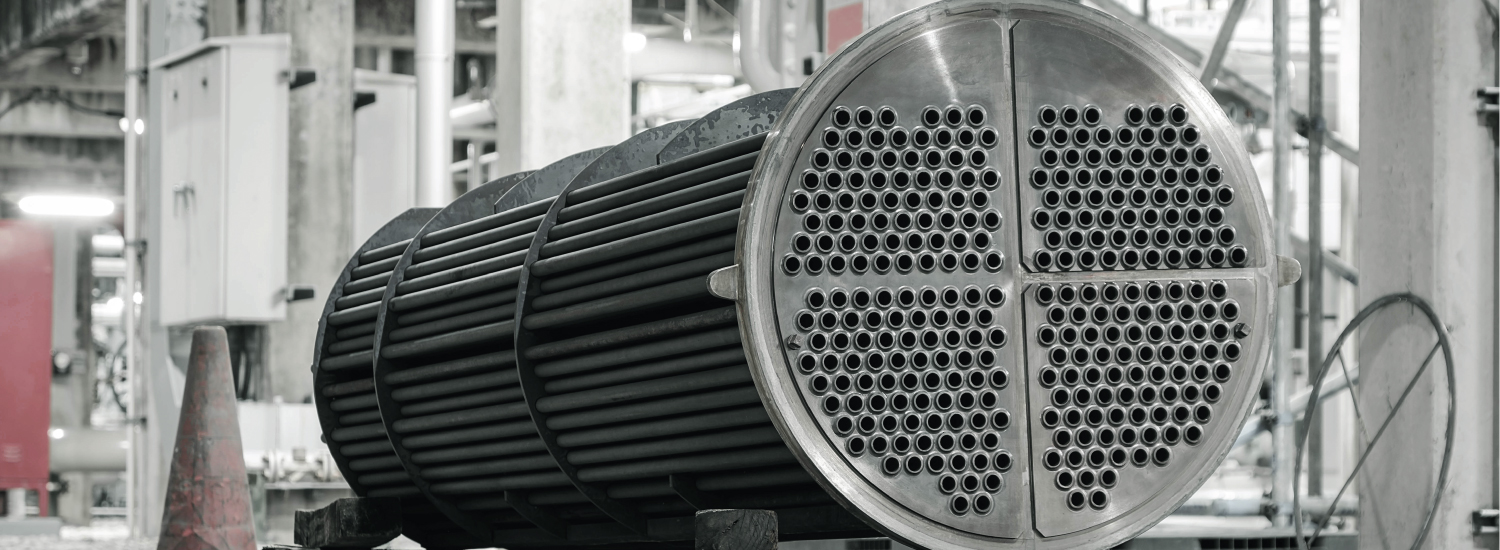
Increase Tool Life On Tough Materials
Benefits of Tapping Spears
In recent years, the use of exotic materials in heat exchanger tubing has become a lot more common. Despite having a higher price tag, these materials are often chosen due to their ability to withstand corrosion and maintain longer tube life. While these materials are great for working in tough conditions, they can have be very challenging to work with as they often require more tooling and job time. This is especially true in tube removal where pulling spears are used. Tapping spears have become an effective way to overcome many of these issues.
While spear pulling has its pros and cons, the largest issue customers face is using them on harsher materials. Monel, Hastelloy, and Duplex are some of the most common exotic materials customers may encounter on the job. Traditionally, spear pulling consists of threading a spear into a tube using an impact drill, then pulling it out with the use of a hydraulic cylinder. However, since these exotic materials have such a high hardness, it can cause premature damage to spear threads when they’re impacted into the tube. Over time, the force of the impact combined with the tube material hardness can wear away the pulling teeth of the spear. This results in poor spear performance and increases consumable costs.
One method that operators have had success with is through using tapping spears on tough applications. A tapping spear is like a pulling spear but has a shorter reach and is manufactured to meet a higher material hardness. The higher hardness allows the spear to hold up longer when used on exotic materials. Note, this is not typically recommended for use in standard carbon steel or stainless applications, as it adds an unnecessary step to the removal process.

Tapping Spear

TT Tube Pulling Spear
To use a tapping spear, the operator should thread it into the tube using a hand wrench or ratchet. This will create the teeth pattern in the tube ID, that will allow the spear to thread into it. Once it’s driven in, the operator can remove the tapping spear and insert a standard pulling spear. The pulling spear should be hand threaded into place to avoid excess wear. With the pulling spear in place, the process can be performed as normal using a hydraulic puller. While this adds an extra step, many customers will have an operator go through with the tapping spear and have another operator following behind with the puller to help speed up the operation.
Using a tapping spear in the removal process can help save on consumable costs, as one tapping spear can cover 50 – 75 tubes. This also helps maintain the pulling spears tool life, allowing the operator to get the most out of the spear before having to switch. This is significantly better than some customers who were getting about 8 – 10 tubes per spear when using the pulling spear on its own.
Overall, exotic materials can make the process of tube removal more challenging. From decreased tool life to increased labor time, the total cost of the job can jump significantly. Incorporating tools like a tapping spear into your process can decrease the amount of labor and costs incurred on these tougher jobs.
Interested in learning more about tapping spears? Contact Elliott today.