How To Retube A Locomotive Boiler
The Unique Design & Common Maintenance Challenges
Historically, many railroad companies used steam locomotives for transportation. Today, most steam locomotives are reserved for private rails, museums, and other charity organizations. As these systems age, they present several unique maintenance challenges that can arise due to the design and location of these units. Understanding the composition of locomotive boilers, as well as the maintenance needs, can make restoration jobs a little bit easier.
One of the most noticeable differences between a standard boiler and a locomotive is the tube sheet pattern. Many early locomotives relied on saturated or wet steam for use in logging and mining operations. While effective, this method of energy production resulted in a lower horsepower output. To make the engine more powerful, super heaters were added to convert the saturated steam into a dry steam, for more energy output. This design resulted in a tube sheet pattern consisting of both 2” boiler tubes and 4 – 5.5” Superheater flues. While this design makes the unit more energy efficient, it can make tube installation more challenging. Since most standard boiler tooling goes up to 3” OD, custom tube expanders are required to fit the flues.
Additionally, tight tube rolling spaces can make it challenging to fit a motor, so universal joints are often used to make it easier to fit into tight corners.
Another space challenge involves inspecting the steam dome at the top of the unit. The throttle body takes up most of the space, forcing the operator to shimmy into a very tight working space. In the event that any work needs to be completed in this area, it can be extremely challenging to fit tooling, let alone a motor due to space constraints.
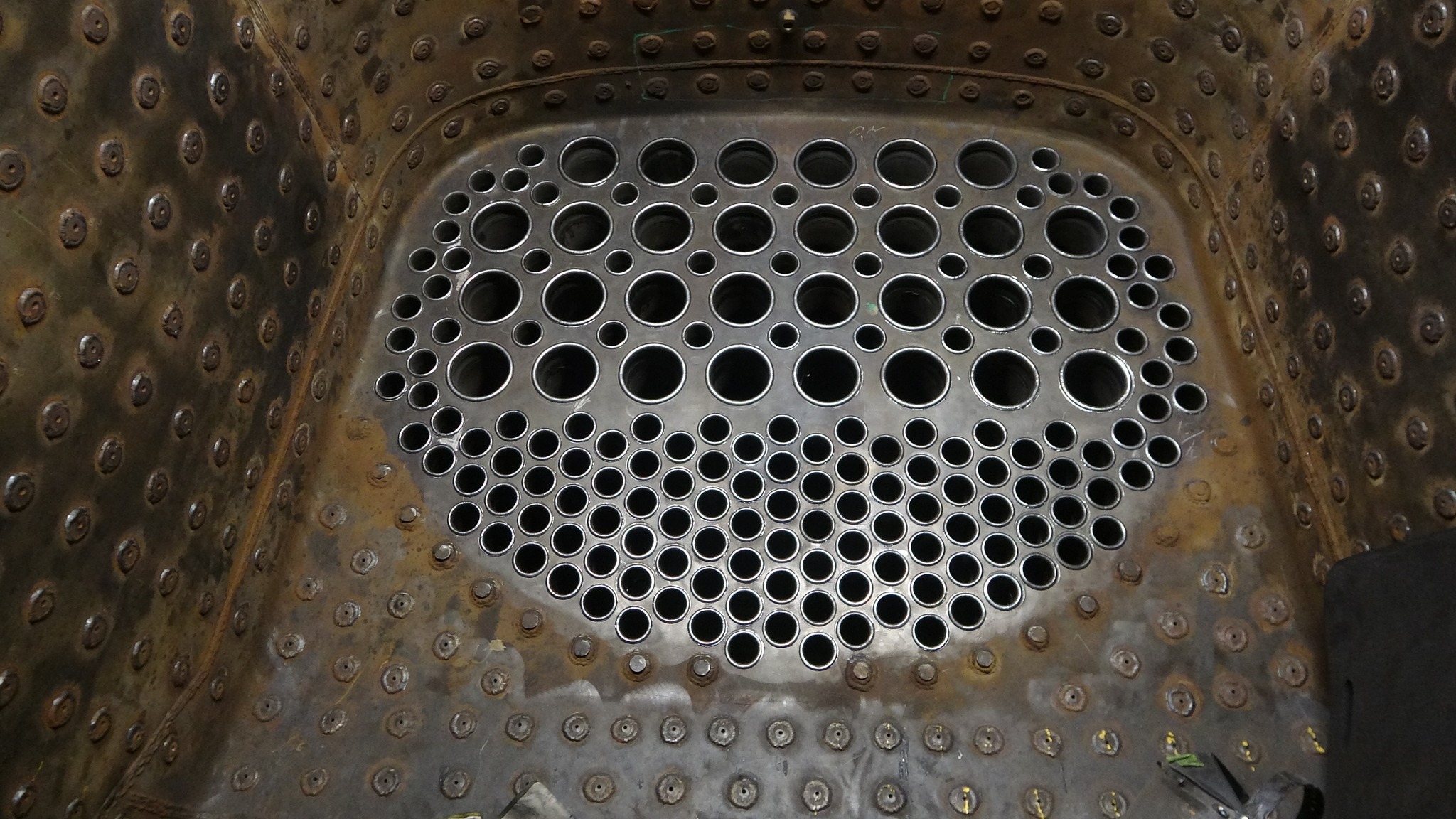
Tube Sheet in a Locomotive Boiler, image provided by Engine 557 Restoration Company
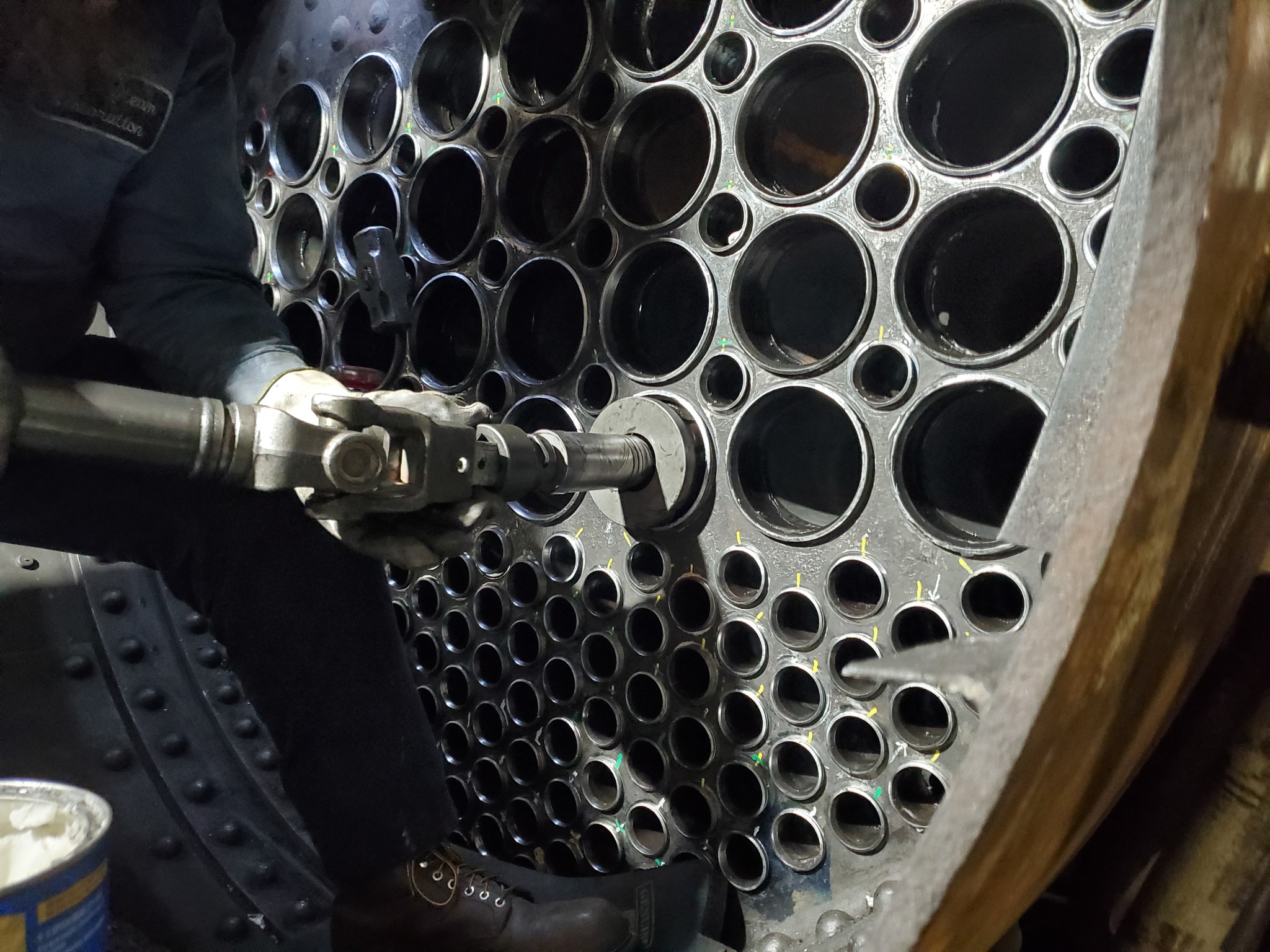
Expanding Flues in a Locomotive Boiler, image provided by Engine 557 Restoration Company
When it comes to routine maintenance of locomotive boilers, the Federal Railroad Administration sets many of the guidelines that these organizations follow. Generally, units must be retubed about every 15 years. This ensures that the entire boiler is up to safety codes and working efficiently. Tube removal is often done using a torch to cut the tube ends on one side of the sheet, followed by the removal of the beaded tube ends. Once the beads have been removed, a seam is cut down the middle of the expanded portion of the tube to relieve the hoop strength, allowing tube stubs to be collapsed and knocked out with an air hammer. On the long side of the tube, a rod and pin style system is used to remove the tube from the sheet. This involves burning a hole in the tube, securing a bolt, and pulling it out using a strap or chain.
Once all the tubes are removed, the tube sheet and other boiler components undergo a full inspection before tubes are reinstalled. Tube sheet holes can enlarge over time and ferrules are often used to prolong the life of the sheet.
In between retubing jobs, boilers will have routine cleanings known as sand outs, where sand is sprinkled in the fire box to sand blast away any deposit or build-up from operation. Flue brushes are also commonly used for the cleaning of tubes. Additionally, periodic inspections are conducted to check for tube leaks or damage. If a tube fails an inspection, it can be plugged until the unit is up for maintenance.
Overall, the design of the locomotive boiler has several differences to a standard boiler, which can present some unique challenges when it comes to maintenance. From the varying tube and flue sizes to working in tight spaces, there are many different factors that come into play when considering tooling and completing maintenance work. Having a better understanding of the maintenance requirements and the options available can help make this process easier.
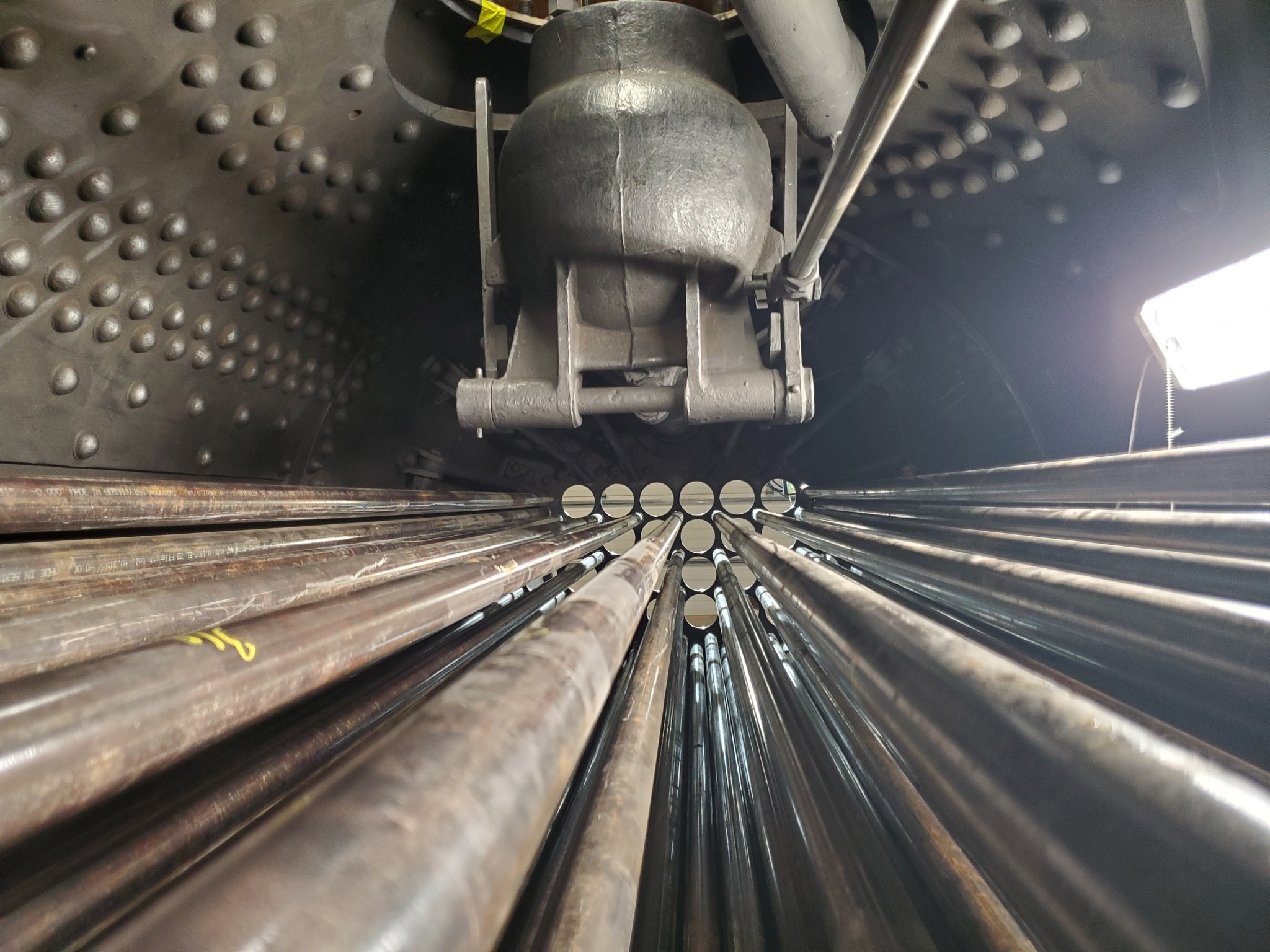
View of the throttle body inside the steam dome, image provided by Engine 557 Restoration Company