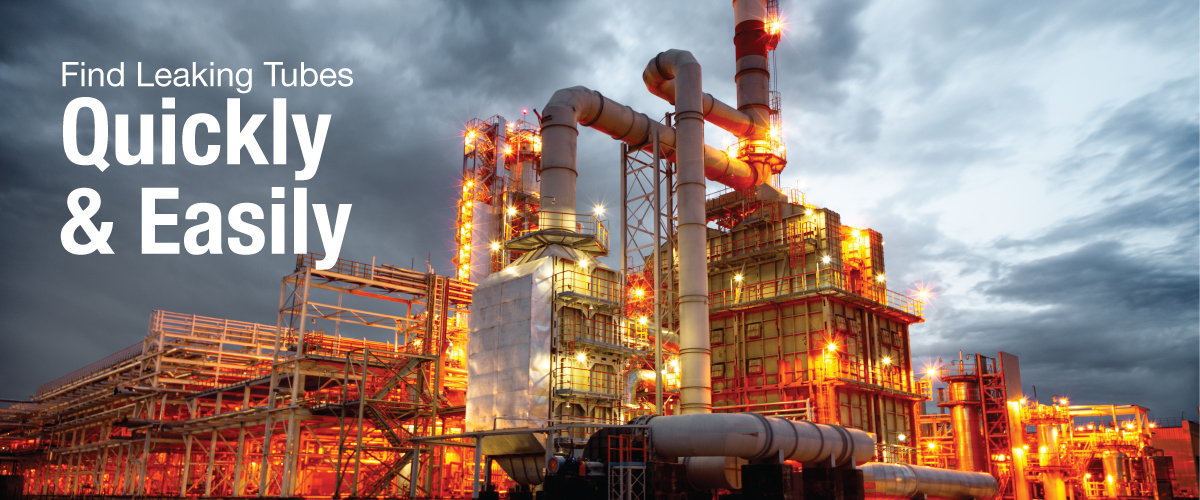
Tubes within vessels need to be regularly tested for leaks for several reasons. Although vessels undergo hydrostatic or eddy current testing after fabrication to ensure proper construction and quality standards have been met, this does not guarantee the vessel won’t develop leaks. Vessels that are in use should be tested when problems are suspected, either from unusual occurrences or decreased efficiency. Vessels in use should also be tested during routine maintenance periods in order to maintain high efficiency and safety standards.
One of the most overlooked best practices for finding tube leaks is to clean the tubes before testing. If the tube is not clean, it is possible for a tube leak to exist, but be covered up by hard deposits or scale. This can result in decreased vessel efficiency later on. Therefore, in order to get accurate test results, make sure the tubes are thoroughly cleaned before testing for leaks.
While tube leaks can occur for numerous reasons, one of the most common causes is the formation of holes. Holes can form within a tube as a result of deposit build-up, corrosion, improper cleaning heads being used, and more. In addition to holes, tube leaks can occur due to joint failures and incomplete expansions. As a result, abiding by installation best practices could potentially reduce the amount of tube leaks that occur within a vessel.
There are several methods of testing for tube leaks. Some small-scale options involve Pressure or Vacuum Leak Test Guns. These handheld test guns are a quick & economical option to detect tube leaks that may be occurring out in the field. Hydrostatic Testing or Eddy Current Testing methods, on the other hand, are usually preferred when testing new vessels in a fabrication environment.
“While tube leaks can occur for numerous reasons, one of the most common causes is the formation of holes. Holes can form within a tube as a result of deposit build-up, corrosion, improper cleaning heads being used, and more.”
Pressure and Vacuum Leak Test Guns are economical, simple to operate, and are useful for checking vessels that are out in the field. Pressure Leak Test Guns create an airtight seal on both ends of the tube, monitoring for drops in air pressure. When using a Pressure Leak Test Gun, simply connect to an air supply, insert a set of seals into both sides of the tube ends and pressurize the tubes. Once the tubes are pressurized, monitor the gauge on the top of the guns for any drop in air pressure. If the seal breaks, that indicates a tube leak is present. Similar to Pressure Test Guns, Vacuum Leak Test Guns create a vacuum tight seal on each tube end. The gun will then monitor for any loss of vacuum, indicating a tube leak. When using a vacuum test gun, first connect to an air supply and then plug one tube end with the test gun and the other end with the Plugging Tool. When you are ready, press the lever to trigger the vacuum system, which will quickly and efficiently evacuates the tube. Again, make sure to monitor the gauge on the gun for any loss of vacuum to indicate a tube leak.
Hydrostatic Testing is most often used in fabrication environments to check new vessels for proper mechanical joints. The vessel is filled with a liquid (usually dyed water) and pressurized to the specified test pressure. Once complete, the vessel is observed for leaks, pressure drops and any changes to the vessel or shape of the vessel. Hydrostatic tests are conducted under the constraints of either the industry’s or the customer’s specifications or may be required by law.
Eddy Current Testing (ECT) is most often used in fabrication to check new vessels for a variety of flaws and ensure high-quality standards. ECT is an electromagnetic testing method that can detect and characterize surface and sub-surface flaws in conductive metals and materials. Different types of tube defects can be detected and sized using ECT, including ID and OD pitting, axial and circumferential cracking, corrosion and tube sheet abnormalities.
Once a leak is found, the best practice is to vent the tube and plug it. Venting is done to eliminate any pressure build-up that may occur and plugging the tube takes the individual tube out of service to ensure the highest vessel efficiency possible.