Precision In Practice
When To Roll To Torque Vs. Size In Mechanical Joining
Mechanical joining is a fundamental manufacturing process used to create a tight seal between tubular products and their corresponding a fittings or flanges. This method relies on compressing the tube’s outer diameter against a fixed container, forming a secure and leak-tight seal. A key decision in this process revolves around whether to roll to size or roll to torque, each of which offers advantages in certain applications.
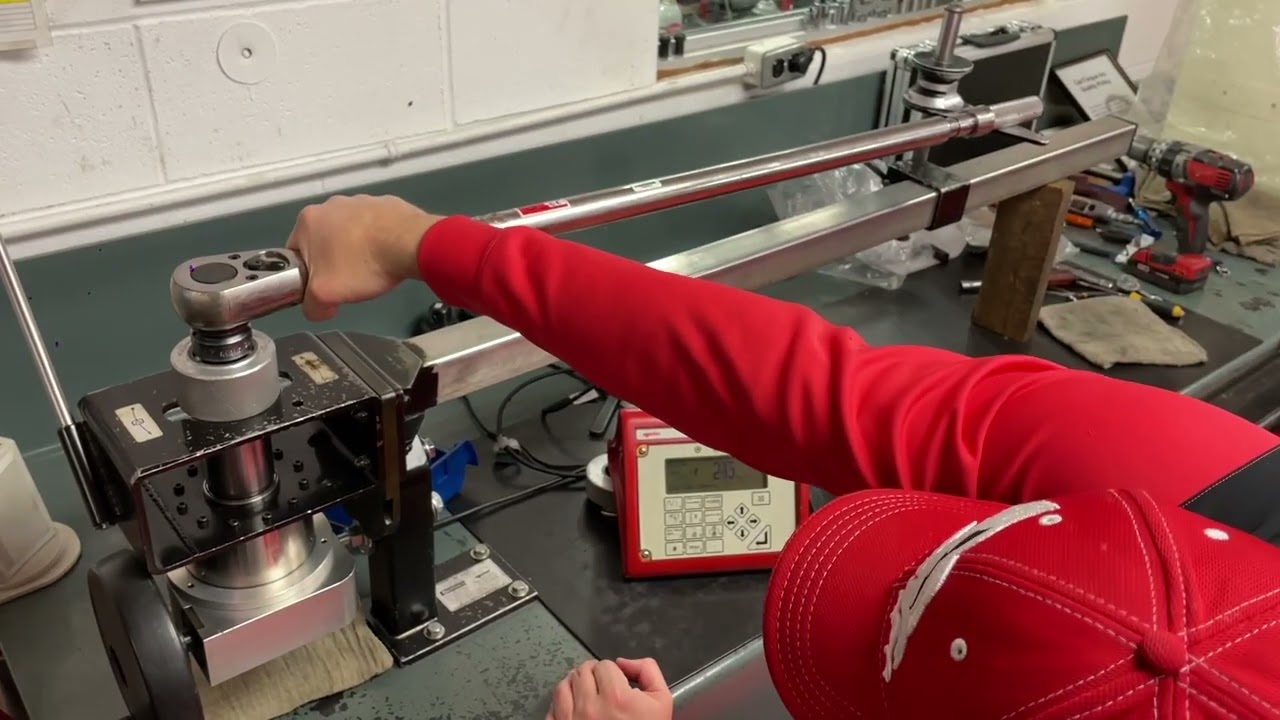
Torque wrenches are another popular and often more accessible option for mechanical joining. These tools, whether utilizing an internal mechanism or an electronic sensor, precisely measure the force being applied. Upon reaching the desired value, the wrench provides a clear digital or audible signal to the operator, indicating expansion is complete.
Regardless of the driving force, rolling to torque compensates for variance in tube sizes, die blocks, fittings, and other manufacturing tolerances. This allows for repeatable and consistent expansions regardless of inconsistencies. The specific torque range required will vary considerably based on the material properties, application, part set-up, and overall manufacturing specifications. In critical applications, extensive testing may be necessary to precisely determine the torque value needed to achieve the desired groove fill for an assembly.
Overall, while rolling to size offers simplicity for less demanding scenarios, rolling to torque provides the precision and consistency vital for high performance and safety critical applications, ensuring a robust and reliable mechanical joint.
Historically, rolling to a predetermined size was the more prevalent method. This technique involves an operator expanding the tube to a pre-calculated diameter, often achieved by visual cues or a set mandrel stop that halts the forward travel of the mandrel. While straightforward, the accuracy of rolling to size is heavily dependent on tight manufacturing tolerances of the components involved. Any variations in tube thickness, fitting bore, or tool dimensions can directly impact the effectiveness of the seal. Consequently, rolling to size is generally reserved for less critical systems and joints where precise groove fill – the extent to which the tube material fills the grooves in the fitting – is less paramount. This is because it’s challenging to determine the exact groove fill for every part.
For parts that will be used in a hydraulic or high-pressure application, rolling to torque is recommended. Rather than rolling to a predetermined finished size, this monitors the amount of force applied during expansion until a set value is reached. Electronic torque control works by monitoring the amperage (amp) draw of a motor and determines the power needed to reach the desired torque value. Once the motor reaches the power requirement, the control will cut power to the motor.
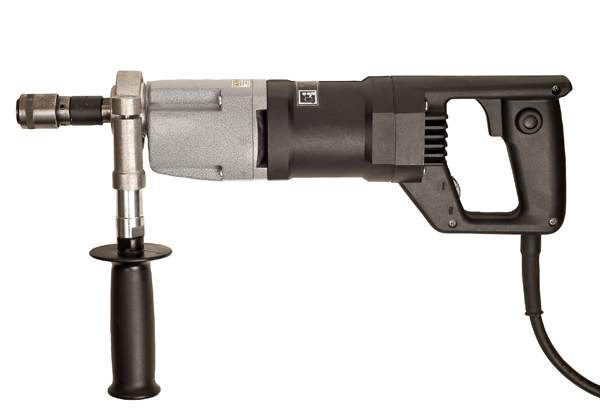
99150 Rolling Series Motor