The Critical Role of Torque in Tube Expansion
Why the Right Motor Matters
For years, tube expansion relied heavily on the subjectivity of “rolling to size or feel”. The issue is that what one operator “sees, hears, or feels” could drastically differ from another, leading to variability and a high potential for error. The advent of torque control revolutionized this process, significantly reducing operator error and ensuring consistent, repeatable results across the board. While torque control is essential for consistency, the success often hinges on one critical factor: selecting the right motor for the job. Understanding why torque matters and the potential pitfalls of choosing the wrong motor is crucial for achieving reliable and lasting tube to tube sheet joints.
The Nuances of Torque Calculation
The torque required for successful tube expansion isn’t a one-size-fits-all value; it takes several key variables into account. While the tube’s outer diameter (OD) and wall thickness are fundamental, the yield strength of the tube material, desired amount of expansion, and the effective roll length of the expander also play a large role.
These additional variables can make a big difference in expansion. For example, the torque needed to expand a 1” x 14 BWG Carbon Steel tube in a 1” tube sheet will be significantly different from the torque required for 1” x 14 BWG Stainless Steel. While Stainless Steel has a higher yield strength, the wall reduction percent could mean a lower torque requirement. It will all depend on the application and the manufacturer requirements.
This inherent variability is why torque guides and reference sheets often present a wide range of specifications. Numerous factors influence the optimal torque, which means you can’t always go off the recommended Tube OD on a chart. Instead, it’s important to understand the specifics of the application prior to selecting tooling.
The Impact of Incorrect Motor Selection
Choosing a motor with insufficient or excessive torque can lead to a cascade of problems, compromising the integrity and longevity of the expanded tubes.
RPM vs. Torque
The first crucial concept to understand is the inverse relationship between RPM and torque. A single motor cannot excel at both ends of the spectrum. High RPMs are generally suitable for expanding small, thin-walled tubes where the resistance and torque requirement are low. Conversely, heavier wall tubes or applications involving thick tube sheets or drum walls necessitate significantly more torque to effectively move the material. This increased torque demands slower rotational speeds.
Insufficient Torque: The Struggle for Expansion
If the selected motor lacks the necessary torque, it simply won’t be able to achieve the desired expansion target. Operators might be tempted to compensate by repeatedly rolling the same tube to reach the target ID. However, this repeated working of the material leads to work hardening. The tube becomes increasingly brittle and resistant to further deformation. Eventually, it will reach a point where no further expansion is possible, resulting in a poor joint that will likely fail hydro testing.
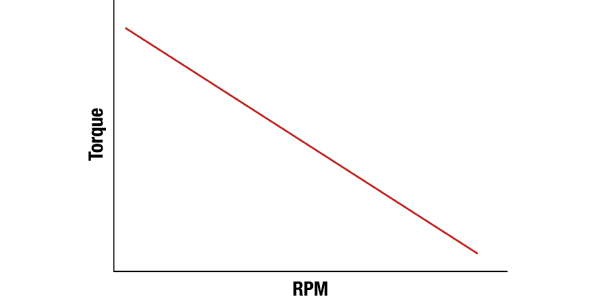
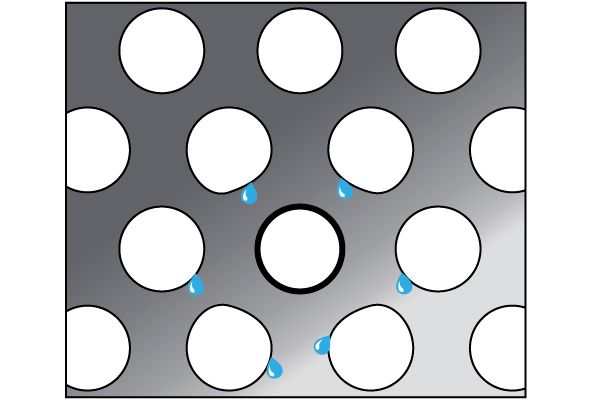
Excessive Torque: The Risk of Over-Expansion
Conversely, selecting a motor with significantly more torque than required can be equally damaging. For instance, if an application demands 7.5 foot-pounds of torque, but the available motor has a minimum threshold of 10-20 foot-pounds, the motor won’t register the lower resistance. It will continue to apply force until it reaches its minimum output, leading to over-expansion.
Over-expanded tubes can become elongated and severely work-hardened. While they might initially pass a hydro test, their long-term performance and durability are compromised. These over-stressed tubes are prone to failure under operational stresses, potentially leading to premature replacement or the need for plugging after only a few months of service. This results in costly downtime and repairs.
Ensuring Optimal Motor Selection
To mitigate these risks and ensure the best possible outcome, it is crucial to collaborate closely with your equipment supplier. Providing them with detailed information about your specific application – including the tube’s OD, wall thickness, material type, and the desired expansion length – will enable them to recommend the most appropriate motor for the job.
Best Practices for Torque-Controlled Expansion
Even with the correct motor, adhering to best practices is essential for consistent and reliable results:
- Pneumatic Motor Considerations: For pneumatic motors, which offer less precise torque measurement compared to electronic systems, it’s advisable to keep detailed records of the torque achieved at each reference mark on the motor. This provides valuable data for future jobs and troubleshooting.
- Start Low and Adjust: It’s always recommended to begin the rolling process with a torque setting that is 1-2 foot-pounds below the recommended target. This approach allows for incremental increases. Remember, you can always increase the torque, but you cannot reverse expansion.
- Expand and Verify: The proper procedure involves rolling a tube, measuring the finished ID, adjusting the torque setting as needed, and then rolling the next tube. This iterative process, with ID checks after each adjustment, ensures accuracy. Once the target ID is achieved, previous tubes can be re-rolled to hit target.
- Regular Monitoring: Once a job commences, it’s important to periodically check the finished ID – ideally every 25-50 expansions. This helps identify any potential change in motor performance or other factors that might be influencing the expansion process.
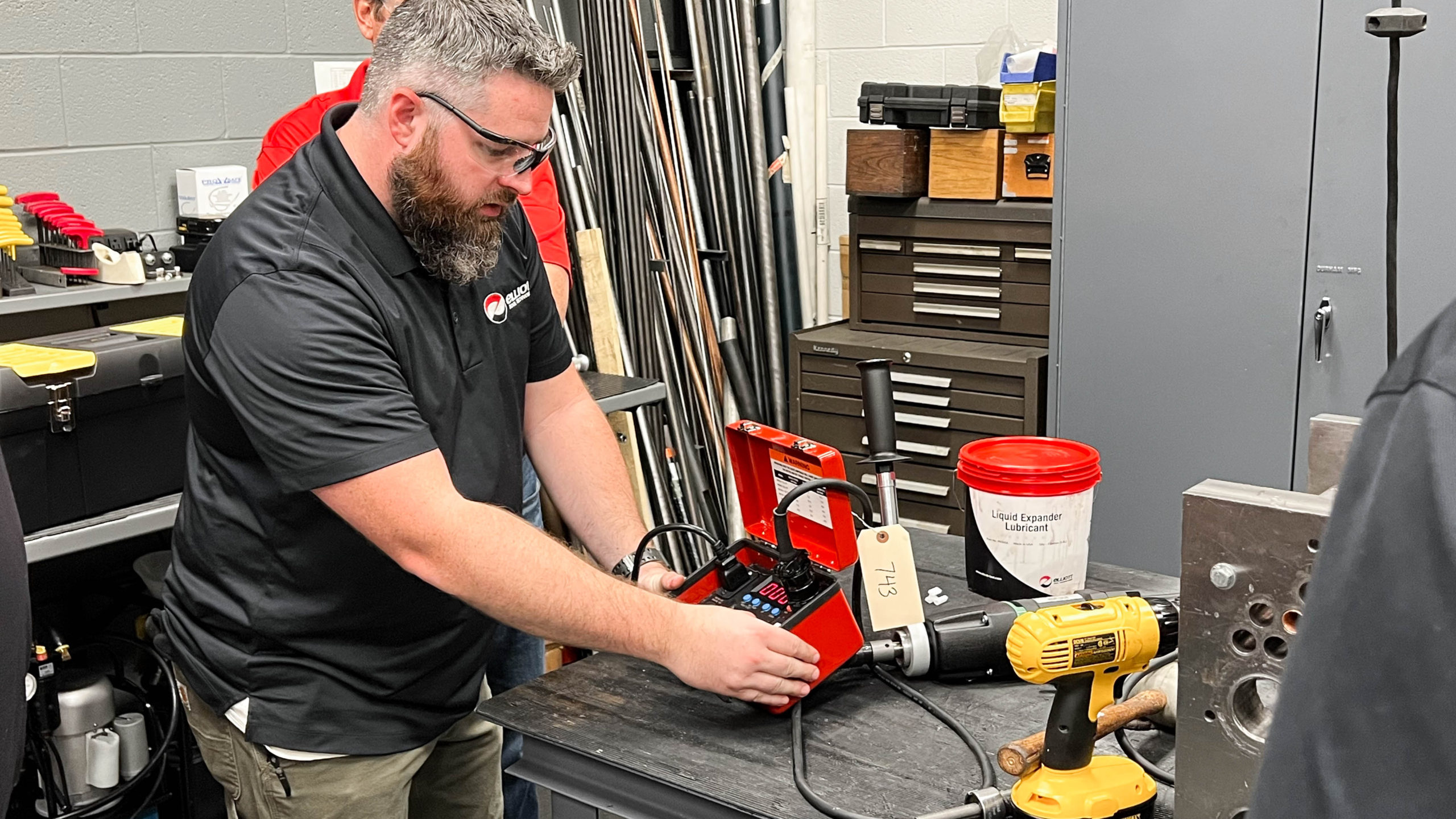
Conclusion
In conclusion, torque is not merely a setting on a motor; it is the fundamental force that dictates the success of the expansion process. Choosing the wrong motor, one that either lacks sufficient power or delivers excessive force, can lead to a host of problems, including inadequate expansion, work hardening, over-expansion, and ultimately, premature tube failure. By understanding the nuances of torque calculation and collaborating with suppliers, operators can effectively utilize torque control to achieve consistent, reliable, and long-lasting tube joints. The investment in the right motor and adherence to best practices are essential for ensuring the integrity and efficiency of heat transfer vessels.