Conquering the Depths: Elliott’s IRU Solutions for Deep Hole Manufacturing Challenges
In precision manufacturing, the creation of recesses in deep holes – those where the depth-to-diameter ratio typically exceeds 10:1 – presents a unique set of challenges. Maintaining accuracy, achieving desired surface finishes, and ensuring efficient chip evacuation become significantly more complex as the bore deepens. Traditional machining methods often struggle in these scenarios, leading to increased cycle times, higher scrap rates, and compromised part quality. However, specialized tooling like Elliott’s Internal Recessing Unit (IRU) offers innovative solutions to overcome these hurdles.
One of the primary obstacles in deep hole manufacturing is chip evacuation and the associated risk of tool breakage. As the cutting tool goes deeper into the workpiece, removing debris becomes increasingly difficult. Trapped chips can lead to clogging, causing excessive friction, tool deflection, and ultimately, catastrophic tool failure. A broken tool deep within a part often results in irreparable damage and costly scrap. Elliott’s IRU is specifically engineered with through-tool coolant delivery, a critical feature for efficient chip management. This design ensures a constant flow of coolant directly to the cutting edge, effectively flushing chips away from the cutting zone. By keeping the blade clean and cool, the risk of chip buildup, tool deflection, and breakage is significantly reduced, leading to more reliable and consistent processes.
Another significant challenge is maintaining bore straightness and minimizing drift. The longer the bore, the greater the susceptibility to tool deflection, resulting in misaligned features and out-of-tolerance grooves. Elliott’s IRU addresses this issue through its precision piloting and rigid tool guidance. This design provides enhanced stability and support to the cutting blade, effectively eliminating tool drift and ensuring consistent alignment throughout the machining operation, even at significant depths.
Achieving tight groove tolerances in deep bores presents its own set of difficulties. Maintaining consistent land diameters and precise groove locations becomes harder to control as the distance from the spindle increases. While IRUs are generally used to create reliefs in existing grooves in deep hole applications, cutting a full groove from solid material in a deep bore requires careful consideration. The increased chip load in such scenarios makes it challenging to achieve the final groove dimensions in a single pass. Elliott’s IRU can be employed effectively in these situations by utilizing multiple cutting steps to gradually achieve the desired groove profile, ensuring accuracy and managing chip load effectively.
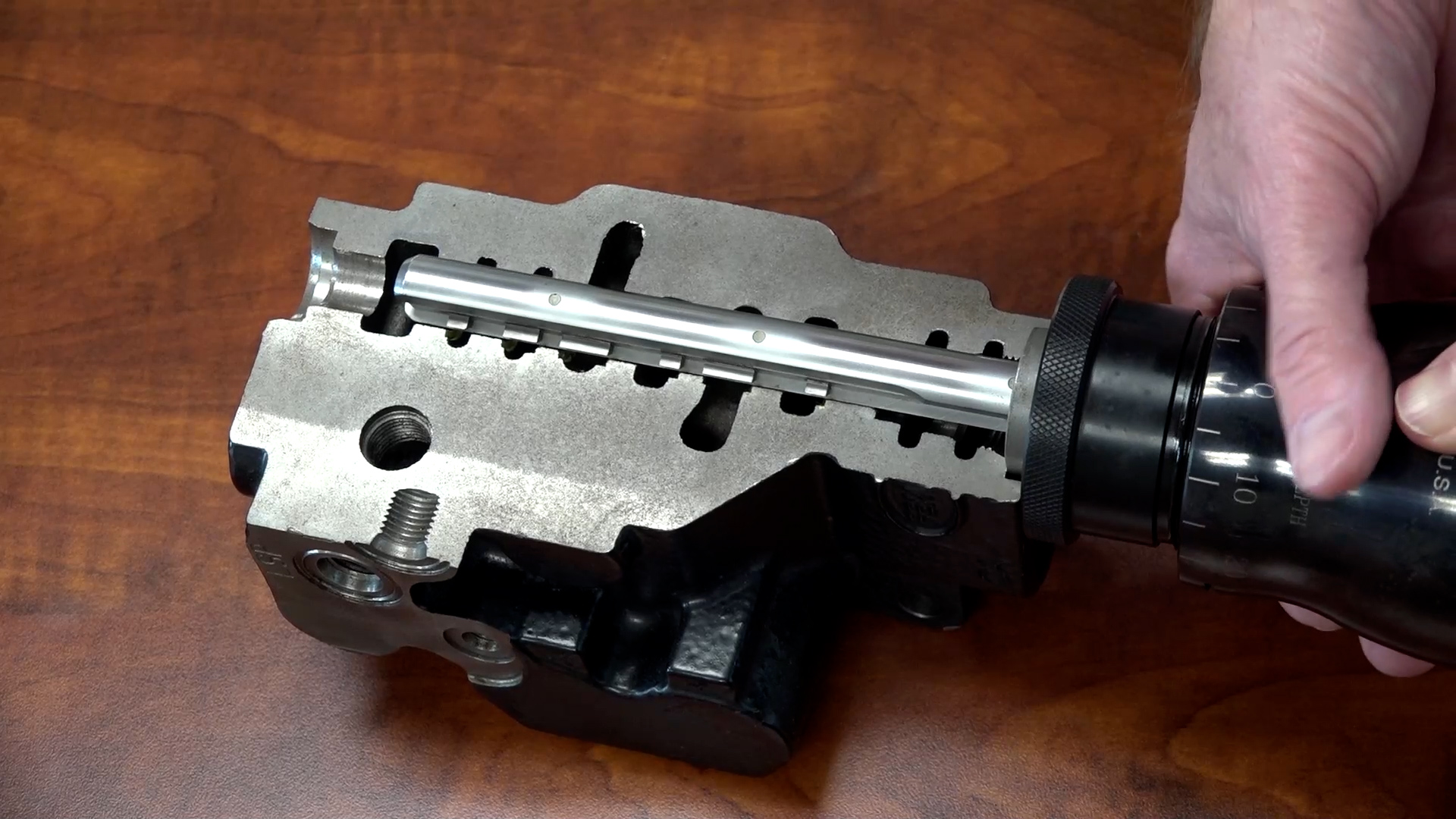
Heat buildup and thermal expansion are also critical concerns in deep hole manufacturing. The reduced coolant access in deep bores can lead to significant temperature increases at the cutting edge. This heat can cause the tool to expand, negatively impacting accuracy and accelerating tool wear. Elliott's IRU incorporates a high-efficiency coolant system designed to directly target the cutting zone. This effective cooling action mitigates heat buildup, maintaining dimensional stability of both the tool and the workpiece, ultimately improving accuracy and extending tool life.
The inherent nature of deep hole manufacturing often necessitates longer tool reaches, which introduces the challenge of tool bending and excessive wear. The increased unsupported length makes the tool more prone to deflection under cutting forces, leading to inaccuracies and premature wear. Elliott's IRU is designed to guide the cutting edge using a precision ground pilot, providing enhanced support and minimizing deflection even with extended reaches. This design consideration helps maintain accuracy over prolonged use and contributes to improved tool longevity.
Finally, vibration and chatter can be significant obstacles, particularly when machining long parts or challenging materials. These unwanted vibrations can lead to poor hole quality and surface finish. Elliott's IRU is engineered to minimize vibration during operation, contributing to a more stable cutting process and reducing the occurrence of chatter. This, coupled with proper workpiece holding techniques to minimize excess movement, ensures a higher quality finished bore.
In conclusion, deep hole manufacturing presents a complex array of challenges that demand specialized solutions. Elliott's Internal Recessing Unit offers a comprehensive approach to overcoming these hurdles through its innovative design features, including efficient chip evacuation, precision guidance, effective coolant delivery, and vibration dampening capabilities. By leveraging the power of the IRU, manufacturers can confidently tackle deep hole applications, achieving improved accuracy, reduced cycle times, and higher quality finished parts.