Mechanical Joining
The Heat-Free Advantage in Aerospace
In the demanding world of aerospace, where precision and reliability are key, the method of mechanical joining stands out as an essential technique. Unlike traditional heat-based joining processes such as welding or brazing, mechanical joining in aircraft systems involves the plastic deformation—specifically, the expansion—of a tube end into a fitting or sleeve. This innovative approach creates a robust, leak-proof joint without the need for elevated temperatures, offering a multitude of benefits crucial to the stringent requirements of aircraft design and operation.
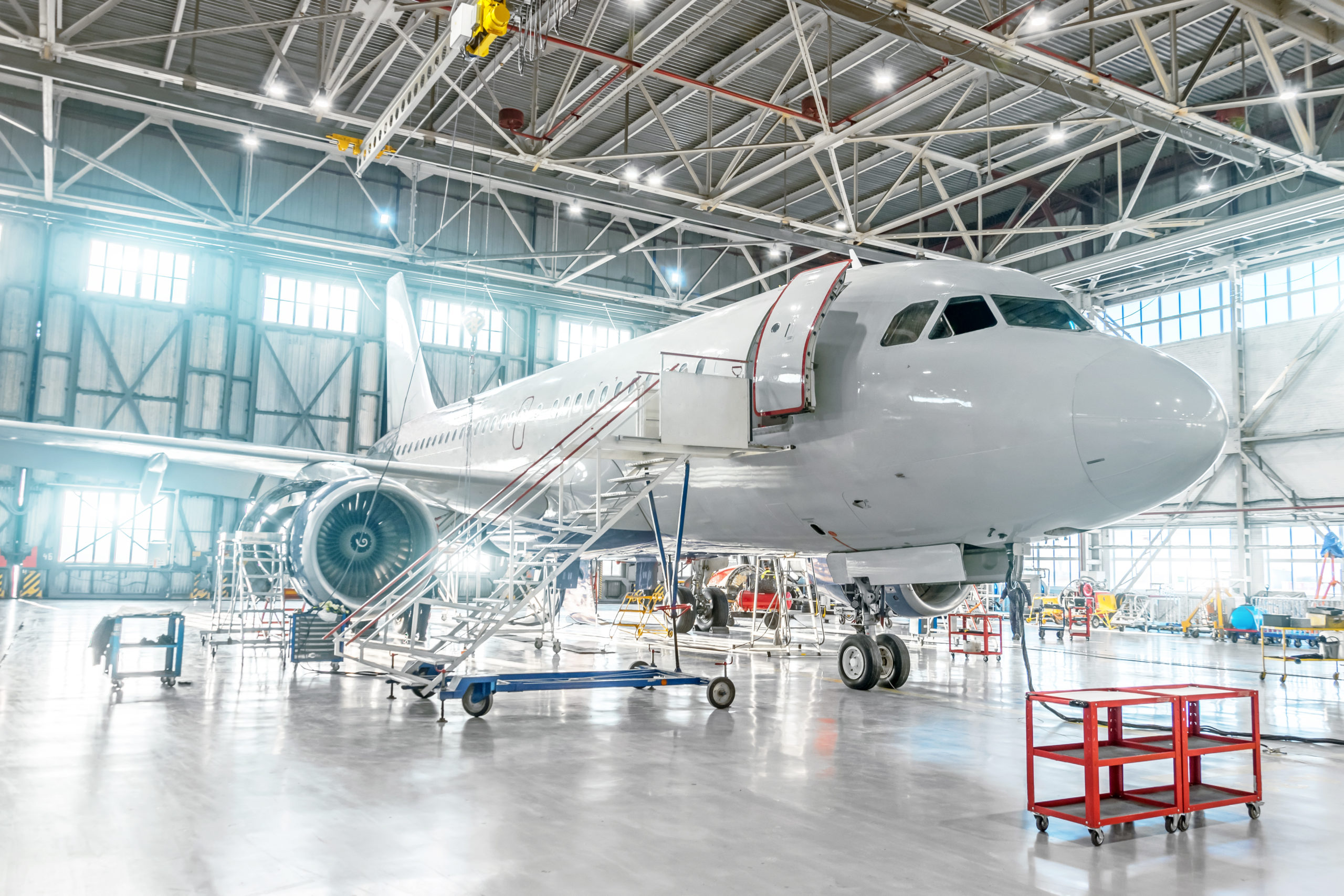
One of the primary advantages of mechanical joining lies in its ability to circumvent the detrimental effects of heat. Many materials commonly used in aircraft, such as aluminum and titanium, are susceptible to heat distortion or changes in their mechanical properties when exposed to high temperatures. Thin-walled tubes, in particular, are highly vulnerable to such damage. Mechanical joining eliminates this risk entirely, preserving the material’s original integrity and strength, which is vital for components operating under extreme conditions.
Furthermore, the process is uniquely suited for applications demanding permanent, leak-tight connections. By plastically deforming the tube into the fitting, a secure fit is achieved. In addition to leak protection, mechanical joints can also withstand up to 20,000 pounds of hydro-static pressure without pulling apart, making them ideal for applications subject to vibration, changes in temperature or altitude, and high-pressure.
The suitability of mechanical joining extends to diverse aircraft systems. In fuel systems, where small-diameter aluminum or titanium tubes are frequently used for fuel manifolds and lines, the expansion process into ferrules or sleeves creates robust connections without the risk of heat distortion common with welding. This is particularly prevalent in rigid fuel lines and engine fuel delivery systems.
High-pressure hydraulic systems also greatly benefit. Here, stainless steel or titanium tubes are commonly expanded into fittings, mitigating the risk of cracking that welds or braze joints might experience under constant vibration. The tight seal created by the expansion ensures system integrity even under extreme dynamic loads.
Similarly, environmental control systems, responsible for cooling and bleed air lines, leverage mechanical joining for its ability to create lightweight, vibration-resistant joints. Thin-walled aluminum tubes are often expanded into couplings or header fittings, contributing to the overall weight reduction that is a continuous goal in aerospace engineering.
Finally, in oxygen and pneumatic systems, where maintaining material integrity is of the utmost importance, mechanical joining of thin-walled aluminum or stainless lines avoids the heat-related issues associated with welding, ensuring the long-term reliability of these life-critical systems.
In essence, mechanical joining offers a compelling combination of material preservation, leak prevention, vibration resistance, and weight efficiency. Its ability to create strong, durable, and heat-free connections makes it an indispensable process, contributing significantly to the safety, performance, and longevity of modern aircraft.
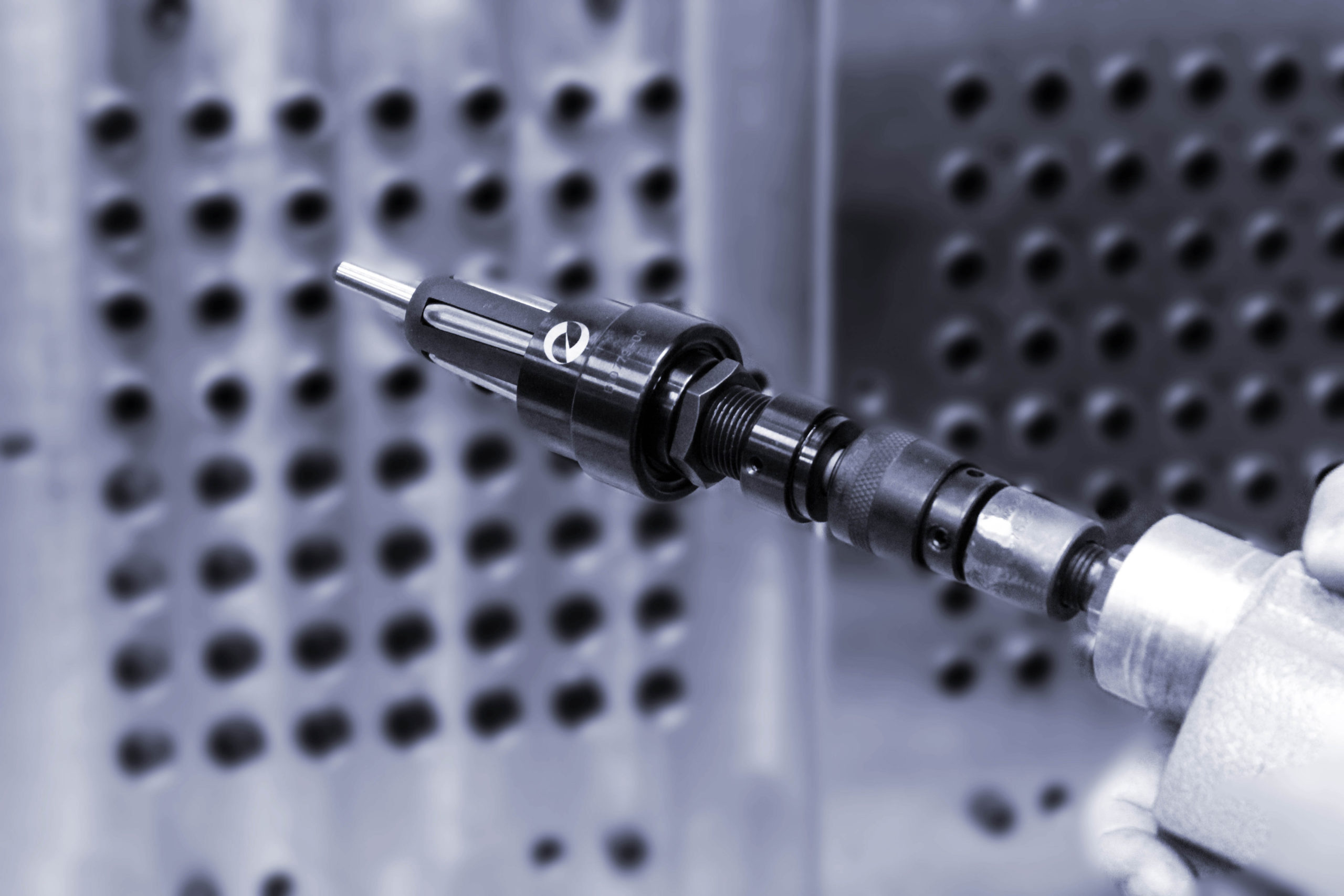