Internal Recessing Unit (IRU) Challenges and Best Practices
Internal Recessing Unit (IRU) Challenges and Best Practices
Internal Recessing Units (IRUs) are specialized tools used when multiple, hard-to-reach grooves need to be machined. Unlike single-point tools like boring bars, IRUs offer advantages in terms of speed and consistency. A single point tool can take a long time and be less consistent in diameter and position of the lands/grooves due to deflection and push off. Also, if the tool breaks, it leaves a partially finished part that needs to be scrapped.
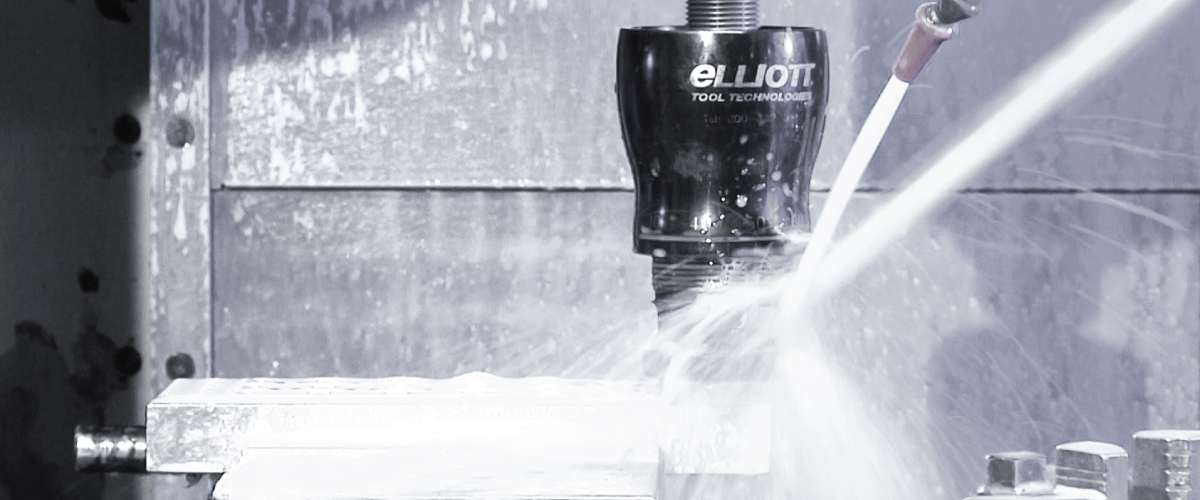
Common Challenges and Solutions
One common issue encountered with IRUs is the failure of the cutter to retract. This can stem from several factors:
- Worn Pull Pin Assembly: Regular use can wear down the pull pin assembly.
- Debris or Chips in the Pilot: Debris build-up can impede proper function.
- Insufficient Lubrication: Inadequate grease in the shank ID of the operating head can restrict movement.
- High-Pressure Coolant: Excessive coolant pressure can prevent blade retraction. In these situations, you need to dwell the tool first.
Another challenge that can impact successful use is the machine the IRU is used on. IRUs typically feature a standard collet chuck with coolant throughput. Using a hydraulic or milling chuck is not recommended due to differing tolerance requirements.
Best Practices for Success
To ensure successful IRU operation, adhere to these best practices:
- Correct Tool Assembly: IRUs are sold and shipped as components. Ensure all components are properly seated during assembly.
- Consistent Bore Diameter: Maintaining consistent bore diameters across parts is crucial for proper IRU function.
- Timely Cutter Replacement: Replace cutters as they wear, indicated by dimensional inconsistencies. A general guideline is to replace cutters every 100-125 minutes of operation.
- Carrier Arm Inspection: While the carrier arm may have a longer lifespan than the blade, inspect it each time the blade is replaced.
- Regular Maintenance: Implement a routine inspection and maintenance schedule for your IRUs.
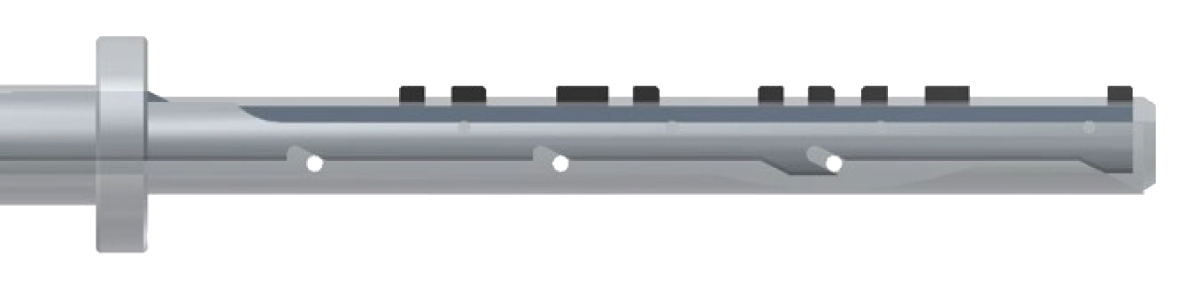
In conclusion, while Internal Recessing Units offer significant advantages for multi-groove internal machining, understanding and addressing potential challenges is key to maximizing their effectiveness. By adhering to best practices in assembly, maintenance, and tool management, manufacturers can ensure consistent results, minimize downtime, and fully leverage the speed and precision that IRUs provide. Regular inspection and proactive replacement of wear components are essential for maintaining optimal performance and avoiding costly scrapped parts.