Cuando los intercambiadores de calor fallan
Comprensión de los mecanismos de falla de los tubos
Los intercambiadores de calor son caballos de batalla en innumerables procesos industriales, facilitando operaciones cruciales de transferencia de calor. Sin embargo, su función crítica a menudo se ve comprometida por fallas en los tubos, lo que genera una menor eficiencia, mayores costos operativos y posibles riesgos de seguridad. Comprender la razón detrás de estos fallos es esencial para realizar un mantenimiento proactivo y garantizar un funcionamiento confiable.
Fatiga térmica y agrietamiento
Los intercambiadores de calor están constantemente expuestos a entornos térmicos dinámicos. Durante el funcionamiento, el arranque y la parada, los materiales dentro del intercambiador de calor experimentan fluctuaciones continuas de temperatura. Estas diferencias de temperatura hacen que el material se expanda y contraiga repetidamente. Con el tiempo, este estrés térmico cíclico puede provocar la formación y propagación de grietas microscópicas, un fenómeno conocido como fatiga térmica. Estas grietas son particularmente frecuentes en áreas con gradientes o restricciones de temperatura significativos, como curvas en U o donde los tubos están soldados a placas de tubos. Con el tiempo, estas grietas pueden convertirse en fisuras más grandes, comprometiendo la integridad del tubo y provocando fugas.
Métodos de detección de fatiga térmica:
La identificación temprana de la fatiga térmica es crucial para prevenir fallas catastróficas. La inspección visual es un método principal que busca grietas visibles o decoloración, especialmente en los puntos de concentración de tensión. La inspección por líquidos penetrantes (DPI) o la prueba de partículas magnéticas (MPT) pueden revelar grietas superficiales que no son fácilmente visibles a simple vista. Para la detección de grietas subterráneas, se pueden emplear pruebas ultrasónicas (UT). Además, el seguimiento de parámetros operativos como las tasas de ciclos de temperatura puede ayudar a predecir posibles áreas de preocupación.
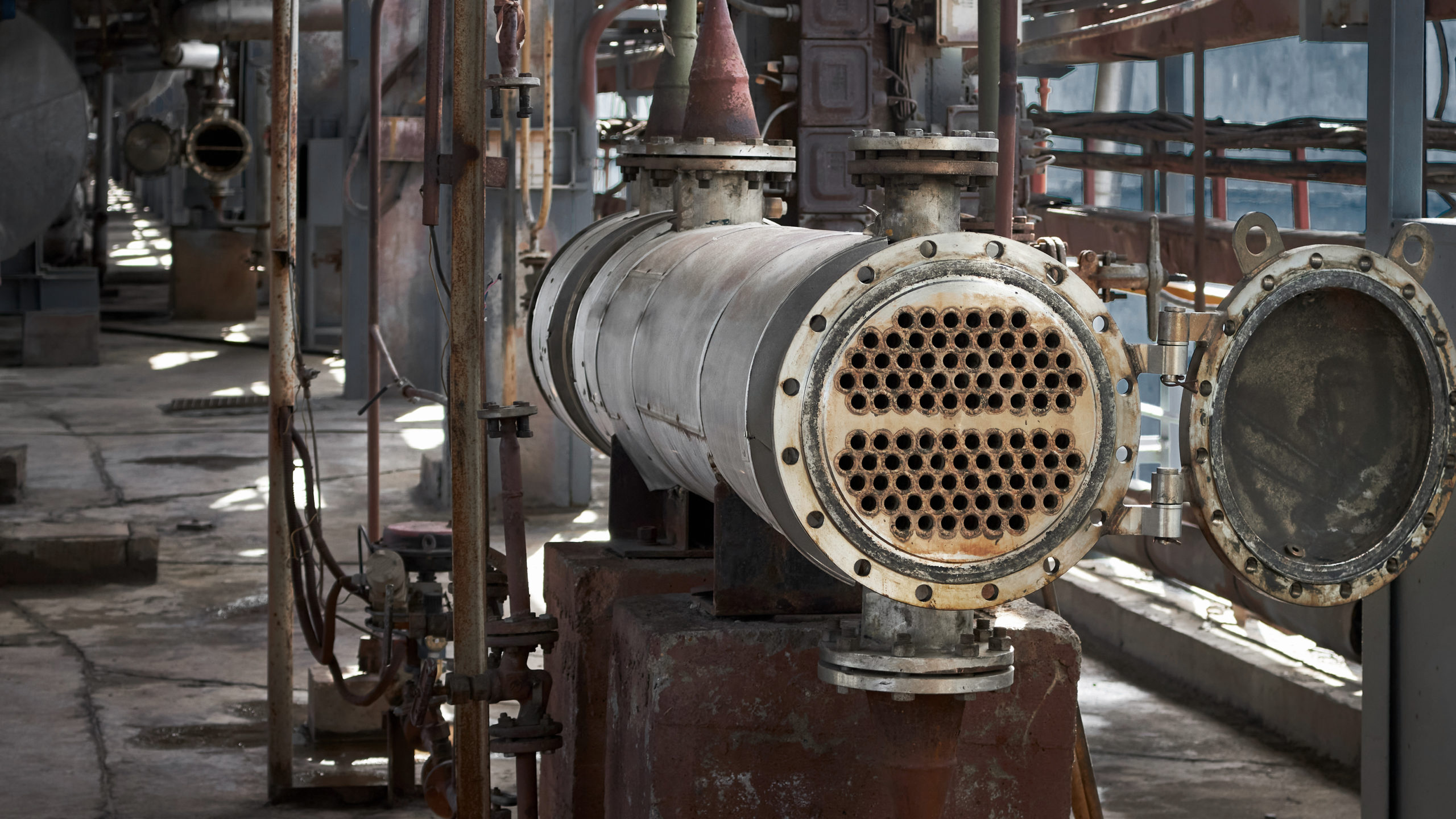
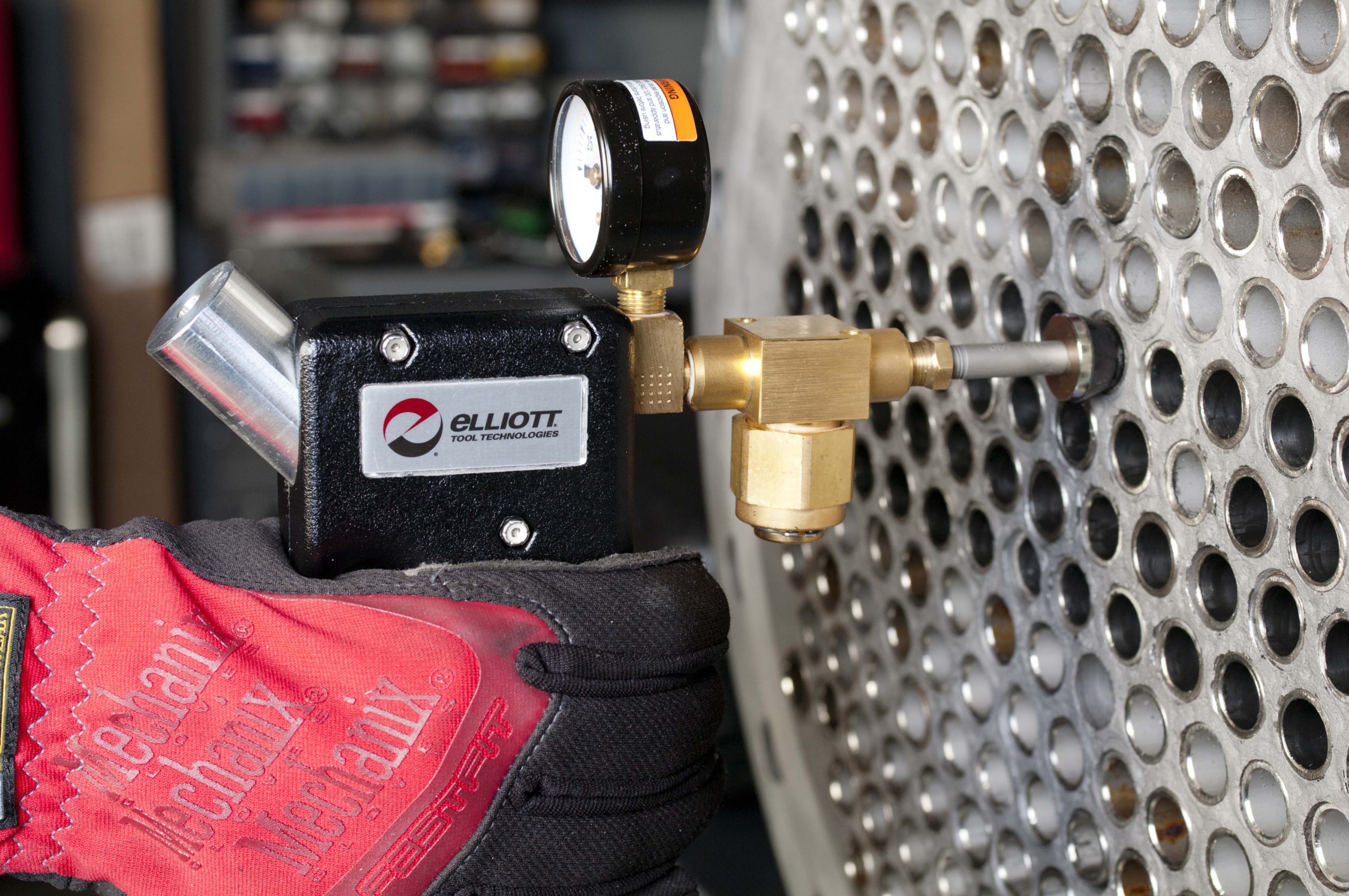
Fugas en los tubos
Las fugas de agua, un tema común y problemático, a menudo se manifiestan como resultado de varias causas subyacentes. Estos pueden incluir la formación de grietas o agujeros en la superficie del tubo debido a la acumulación de depósitos, lo que crea entornos corrosivos localizados. De manera similar, la corrosión general, la erosión causada por altas velocidades de fluido y partículas abrasivas, o incluso métodos de limpieza inadecuados pueden adelgazar la pared del tubo, haciéndolo susceptible a fugas. Una vez que se forma una fuga, puede afectar significativamente la eficiencia del intercambiador de calor, ya que los fluidos evitan la ruta de transferencia de calor prevista. Más críticamente, si se mezclan fluidos de diferentes corrientes, pueden producirse reacciones peligrosas o contaminación, lo que representa un riesgo de seguridad significativo.
Más allá de los factores operativos, los errores de fabricación e instalación también contribuyen significativamente a las fugas en los tubos. El laminado insuficiente durante la fabricación se produce cuando el tubo no se expande lo suficiente en el orificio de la placa tubular. Esto crea una posible ruta de fuga entre el diámetro exterior (OD) del tubo y el diámetro interior (ID) del orificio de la placa del tubo. Por el contrario, el laminado excesivo se produce cuando el tubo se expande más allá de la reducción de pared requerida. Esto puede dañar gravemente la placa de tubos o los tubos adyacentes. Cuando un «ligamento» de una placa tubular (el material entre los orificios de los tubos adyacentes) se enrolla demasiado, puede deformar los ligamentos de las articulaciones circundantes, lo que induce tensión y provoca fugas. Esta deformación generalizada aumenta drásticamente la susceptibilidad de toda la placa tubular a sufrir fugas, lo que genera mayores costos de reparación y caídas persistentes de la eficiencia.
Métodos de detección de fugas en tubos:
Se utilizan varios métodos para localizar fugas en los tubos. La prueba de presión o vacío es un método manual sencillo que se puede utilizar para identificar una caída de presión o una fuga en un tubo. La detección de fugas de helio es un método altamente sensible en el que se introduce gas helio en un lado y un detector en el otro lado identifica el helio que se escapa. Por último, la prueba hidrostática es un método común utilizado después de la fabricación, en el que se llena un recipiente con agua a presión y se monitorea para detectar posibles fugas en las juntas.
Falla mecánica
La falla mecánica en los tubos del intercambiador de calor es una categoría amplia impulsada por factores como la vibración, la instalación incorrecta y el estrés operativo.
La vibración excesiva es un culpable omnipresente. La vibración inducida por el flujo, que surge de la interacción entre el flujo de fluido y los tubos, puede provocar desgaste de los tubos y fallas por fatiga. El desgaste de los tubos se produce cuando los tubos se frotan repetidamente contra estructuras de soporte, como deflectores, o incluso contra tubos adyacentes. Esta fricción constante erosiona gradualmente el material del tubo, lo que provoca su adelgazamiento y eventual perforación.
Por otro lado, la falla por fatiga es resultado del estrés cíclico continuo impuesto por la vibración. Incluso si los niveles de tensión individuales están por debajo de la resistencia al rendimiento del material, la exposición prolongada puede iniciar y propagar grietas por fatiga, particularmente en puntos de concentración de tensión, como curvas en U o áreas con cambios geométricos pronunciados. Si estas grietas no se identifican y se abordan a tiempo, pueden crecer rápidamente y culminar en rupturas catastróficas de los tubos.
Más allá de la vibración, un diseño o una instalación inadecuados pueden crear debilidades inherentes. La selección incorrecta de materiales, estructuras de soporte inadecuadas o problemas en las uniones entre tubos y placas de tubos durante la fabricación pueden generar «puntos débiles» susceptibles a un desgaste prematuro o incluso a una falla repentina y catastrófica en condiciones normales de funcionamiento.
Métodos de detección de fallas mecánicas:
La inspección visual puede revelar signos de roce o deformación. La prueba de corriente de Foucault (ECT) es muy eficaz para detectar grietas por fatiga, adelgazamiento y picaduras en tubos no ferromagnéticos. La inspección visual remota (RVI) mediante boroscopios permite el examen interno de los tubos. El análisis de vibraciones y el análisis modal pueden identificar frecuencias de resonancia y predecir posibles problemas de vibración. Para problemas de mayor escala, las pruebas hidrostáticas pueden revelar fallas mecánicas graves al someter todo el recipiente a alta presión.
Al comprender estos mecanismos de falla distintivos y emplear métodos de detección adecuados, las industrias pueden mejorar significativamente la confiabilidad y la vida útil de sus equipos críticos de intercambio de calor, protegiendo tanto la eficiencia como la seguridad.
Para obtener más información sobre fallas de tubos debido a la corrosión y erosión, consulte xyz en nuestra serie.